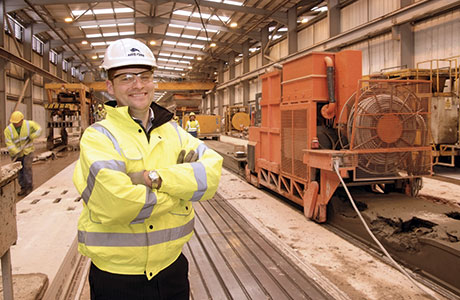
JIM Harley, Operations Manager at Bison Manufacturing, is celebrating 25 years with the manufacturers of precast concrete products this year.
In that time he’s worked in the concrete lab, drawing office, factory, planning office and contracts department.
He’s the definition of the phrase “working your way up the ranks”, having initially joined the company’s Falkirk base straight from school.
“I really wanted to join the RAF,” Jim said. “I passed the assessment but they weren’t recruiting so I went for an interview with Bison in Falkirk. Six months later the RAF got in touch to say they were taking on new recruits but I turned it down. My mentor, the chief engineer, had taken me under his wing and I was enjoying what I was doing.”
Jim spent his first few years moving from department to department, learning the business inside out. This grounding enabled him to see first-hand the challenges faced by each division – something he reckons would benefit young workers in the industry today.
“I had a good learning curve,” Jim added. “I started in the lab doing things like testing materials and quality checking. Then I moved to the drawing office and was interfacing with customers. Eventually I had a role which involved me going round sites.
“Bison put me through a civil engineering college course. It was great experience to see every part of the business.”
Jim eventually became Operations Manager at Bison’s Falkirk factory and when the Uddingston base opened in 2001, he took on a similar role there.
“That was the start of a long-term plan,” Jim recalled. “We’re not too far from Ravenscraig so there was no problem recruiting quality workers.”
Today the company is thriving but Jim admits there were some tough moments following the recession when the factory was only operating at 50% production at one stage.
“Having to make people redundant who’d worked for the company for 40 years, and whose fathers worked here before them, was hard,” Jim added. “The business survived but it was hard going.
“Between 2001 and 2008 we were operating at 95% capacity seven days a week. After 2008 this reduced to 50% over five days. For many of our customers at that time, every penny counted so some were going with the cheapest provider and that was killing us.
“We’ve always been more focused on quality. But we decided to stick to the standards taught and not scrimp on quality. Thankfully people are now coming back to us.”
Things are on the up again. In the first half of 2013 the Uddingston factory was up to 75% production, thanks in part to a lucrative contract to produce more than 40,000 square metres of flooring for the new terminal at Heathrow Airport.
In order to meet the airport’s requirements, Bison had to develop flooring slabs 60mm deep – the thinnest to be manufactured in Britain.
“That project was a lifeline,” Jim added. “I like driving back to something and saying “we’ve built that”. I have a passion for manufacturing.”
Jim is confident the future is bright for Bison, and points to the emerging recovery of the housing market as grounds for optimism.
“Until 2008, 75% of our work went into housing. Today that figure is 25% as we do more in sectors such as education and public sector projects. For a while no houses were being built so we had to focus elsewhere.
“But as soon as the housing market grows, we hope to have more factories. We’re also looking to develop the land we have here.”