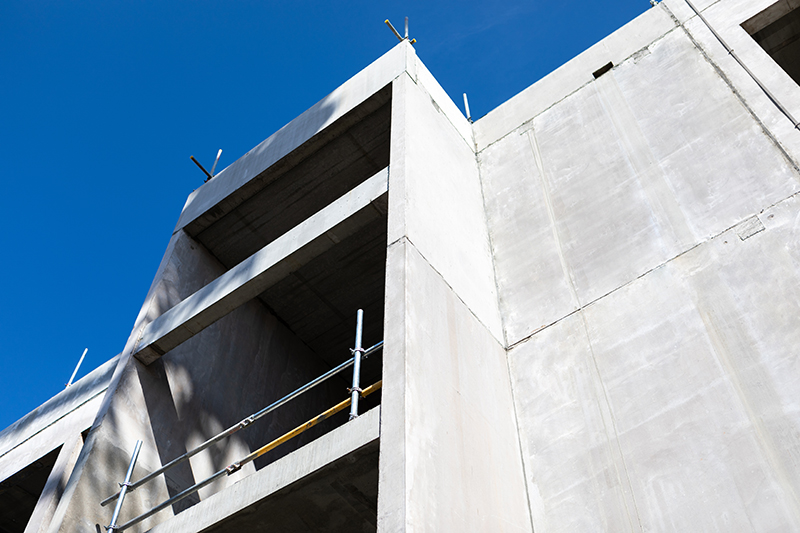
A precast concrete approach to constructing the building frame for the UK’s largest ever Passivhaus school has demonstrated the material’s potential for use in highly sustainable buildings. Mark McCann from precast concrete products manufacturer FP McCann explains why.
THE development of a new educational campus has shown how precast concrete could play an increasingly important role in the construction of public buildings designed to meet the highest sustainability standards, and help the UK to achieve its net zero carbon goal.
The recently opened £120m Dunfermline Learning Campus primarily replaces two schools which had reached the end of their lifespan and no longer met the needs of 21st century education. The project to replace Woodmill High School and St. Columba’s RC High School was initiated by Fife Council in 2019 with the aim of bringing together the two secondary schools into a single building. It would also enable a new facility for Fife College to be integrated into the site to create a new education hub as part of a wider masterplan.
Rather than adopt a compliance-level approach where the new building would meet the current Building Regulations and school design standards, Fife Council had much more ambitious goals to create a state-of-the-art facility. In addition to ensuring the two schools would retain their individual identities, Fife Council sought to create a number of high quality shared facilities to enable progressive teaching and the cross-fertilisation of ideas in a building designed to push the boundaries for collaborative working.
Energy reduction and sustainability were high priority too, with Fife Council stipulating design to achieve Passivhaus Classic Certification, whilst also setting a low embodied carbon value for the project, as per RIBA 2025 targets. In addition, this was one of the first construction projects to apply the Scottish Government and Scottish Futures Trust’s new ‘Net Zero Public Sector Buildings Standard’, a voluntary standard designed to support public bodies to define objectives for their construction project in pursuit of a credible path to net zero operational energy.
Focus on the building form
AHR Architects were tasked with designing the new building to accommodate Woodmill High School and St. Columba’s RC High School. Its Glasgow team worked closely with Fife Council’s architect John Peden to bring the vision to fruition and main contractor BAM Construction, who have delivered a number of previous projects for the council including Madras College in St Andrews.
AHR recognised the importance of embracing key Passivhaus principles from the outset, firstly in respect of the building form. In Passivhaus projects, the ‘form factor’ must be considered to ensure the ratio of the external envelope to the floor area is minimised, thus lowering the potential for heat loss. This resulted in a design with the accommodation arranged over three floors and a relatively compact form which avoided complexities such as external soffits and multiple steps in the massing.
Simplification of the build process was also significantly important for a building of this scale. In particular, how to ensure the building’s main frame could be built most efficiently whilst also achieving super-high levels of airtightness.
An analysis of the frame options was undertaken early in the design at RIBA Stage 1-2 to assess which approach would achieve the airtightness level of 0.6 air changes per hour (ACH), expressed as ≤ 0.6 h-1 @ 50 Pa. From this, the decision was made to adopt three different methods. Precast concrete was selected for the main building frame, CLT (cross laminated timber) was chosen for the sports block and a hybrid steel frame as used to form the core of the building.
Delivering on precast concrete’s airtightness promise
Choosing precast concrete for the main building frame maximised delivery of an airtight envelope and simplification of detailing. This is because concrete is in itself inherently airtight, which makes it easier to track the airtightness line through the building, and it does not rely on membranes and tapes throughout the line.
In addition, because the joints between the precast panels could be pressure grouted, this further assists in maintaining an airtight line. Also, in general, concrete allows the airtight line to be on the internal face of the panels, allowing for ease of tracking and resolution of any issues throughout the build.
The theoretical advantages of using precast concrete, however, still required translating into reality, and this is where the expertise of BAM Construction and FP McCann came into play. We had to ensure approximately 1,500 units including precast walls, ‘Hellerup’ stair, stairs, lift shafts, floor planks and columns were manufactured to the highest quality standards and delivered to site and installed with maximum efficiency.
The precast concrete frame was built over a 27-week period between October 2022 and May 2023, with a large crane lifting the panels into position on arrival to site from our Byley factory in Cheshire. Some of these precast panels were particularly large, with seven measuring 12m in length for the construction of the three storey high dining hall.
Quality focus key to success
For BAM Construction, the project was the first Passivhaus build of this type they had undertaken in Scotland, but they were able to draw on extensive experience from within the group, chiefly in respect of projects in South West England and Germany. Their approach from the outset was to create the pre-cast structure not just to be ‘a little bit more airtight’, but significantly so.
The BAM team in Scotland recognised that the key difference between this project and non-Passivhaus building projects was intense scrutiny on quality and detailing, and the initial advice provided by their colleagues in Germany was simply put – ‘build it with concrete’. By using this material, they knew they could create an inherently airtight frame that would not have to rely on membranes and other elements.
Quality control was critically important to ensure the airtightness goals would be achieved and the project team developed processes to manage this. Fife Council’s architect, John Peden, took on the role of “quality champion” and established a quality team. They sought to look for continuous improvement opportunities, including using lessons learned from previous projects, through dedicated quality meetings on site, quality walk-rounds, and by reviewing particular elements of work as it began or prior to roll-out.
The result of this attention to detail and continuous quality focus delivered an airtightness level that surpassed the target. In the precast concrete framed building, airtightness of 0.4 h-1 @ 50 Pa was recorded.
A very high level of airtightness was not the only benefit of using precast concrete, however. Superior acoustic performance could be achieved more easily due to the floor-to-floor spans of the precast units, and they also reduced the need for linings in the stairwells, which is a vulnerable area.
Precast concrete also enabled the building envelope to be partially wind and water-tight much earlier in the programme than would have been the case with other approaches, such as a cladding solution. This in itself has major benefits, not least helping to keep the build schedule on track amidst the uncertainty of the Scottish weather.
Lessons for future Passivhaus projects
Applying Passivhaus principles to the construction of the new Woodmill High School and St. Columba’s RC High School was an ambitious step by Fife Council, but it has delivered outstanding results thanks to the positive approach of the whole project team and a dedication to design quality. Architect’s AHR balanced the need to embed Passivhaus principles with quality from the outset and the selection of materials, including precast concrete, contributed to achieving high thermal and acoustic performance.
Buildability was also significant in this project and here again precast concrete proved its value. The architects acknowledged that the decision to go with this material for the main building frame helped to make the build process straightforward. This in itself can have a massive impact on the success of construction projects because complexity is reduced and efficiency is therefore improved.
But one of the most important outcomes of this project is that it challenges the perception of concrete not being compatible with highly sustainable construction. The benefits of precast concrete over the lifetime of these school buildings, particularly in respect of helping to minimise energy consumption for heating and cooling will far outweigh the carbon emissions resulting from the production of its raw materials and its manufacture.
Find out more about the benefits of precast concrete at www.fpmccann.co.uk.