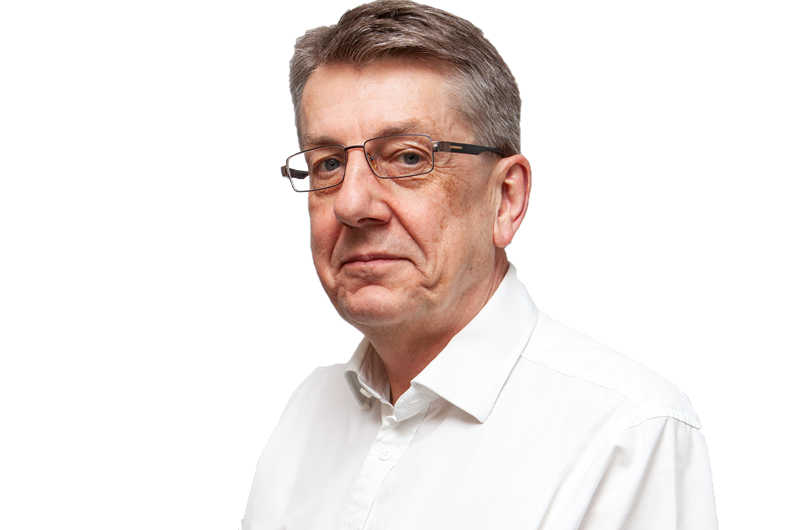
Steve Roebuck, European health & safety director at West Fraser explains why achieving net carbon negative status for the products is not the end of the company’s environmental journey
West Fraser, and formerly Norbord, has always been committed to reducing the impact of our operation on the environment. All of our products are produced in the UK using Woodland Assurance Scheme wood from sustainably managed forests.
Aside from the raw material supply side of our operation, we have been focused on the energy we use. Our industry is in the energy-intensive category, so West Fraser is one of a number of big energy users.
Wood is 50% water when we buy it and this requires a good deal of heat to dry it out. We’ve taken steps to counter the impact of this high energy consumption by focusing on fossil fuel energy. We now derive 1455 GWhr (2021) of heat from renewable sources, principally process residues, with anything left over from the manufacturing process being used to generate heat, making West Fraser the largest of industrial generator of renewable heat in the UK.
All three of our UK sites participate in the government renewable heat incentive scheme. To be able to participate in that the material that’s used to generate heat must be from renewable sources. This has been verified through annual independent audit and certification.
The other high energy demand of our industry is on electricity, and we have just entered into contracts with our electricity providers to ensure all our electricity comes from renewable sources. This means we only buy renewable electricity, covered by REGO guarantees (renewable energy of guaranteed origins). There is a premium to pay for that, but we think it’s the right thing to do.
We’ve also installed low energy LED lighting with motion sensors across our sites!
Indeed, our company has globally committed to reduce greenhouse gas emissions by 2030. This means our targets are aligned with the less than 1.5˚C temperature rise. The company has committed publicly to these targets and is committing $50million a year to achieving them.
Our impact on the environment matters to us. As well as a global commitment by the company, we are always looking for ways we can reduce our carbon footprint closer to home, and this often means financial investment.
Our OSB is manufactured in Inverness and all our wood comes from within an approximate 70-mile radius of the factory. At the moment, virtually all of the OSB manufactured in the Inverness plant goes out by road, but right now we are in a capital process with Network Rail.
We’ve run trials and are in the process of building the capital infrastructure to be able to switch to rail and that will have a massive impact on transport emissions. By switching from road to rail we estimate that we will make a saving of around 9,000 tonnes of Co2 a year.
So, although we are proud of the net carbon negative status of our products there is always more that we can do, and we are committed to doing what we can to ensure we don’t detrimentally impact the planet we all live on.