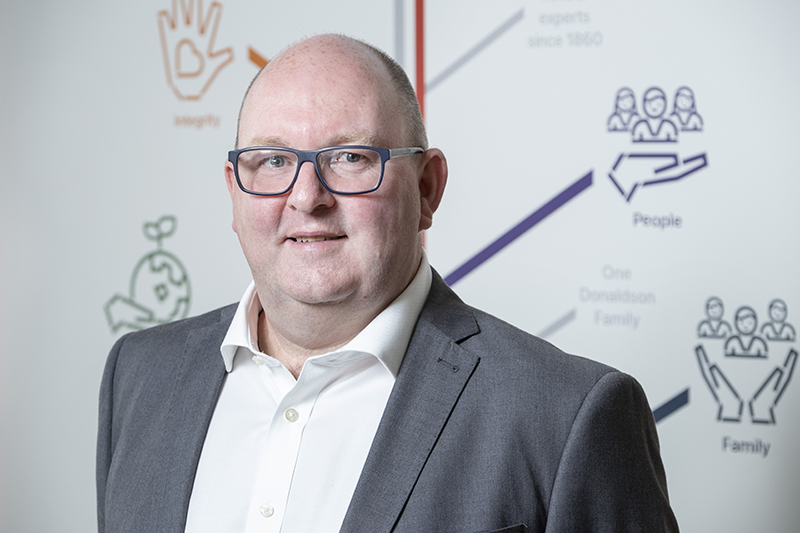
The role of sustainability in business is constantly evolving, but as Mark Murphy, chief risk officer at the Donaldson Group explains, it should always be a top priority.
‘Always do good.’ This was the message that was ingrained in me from the day I started at the Donaldson Group 38 years ago.
Sustainability has been at the heart of our business for a long time, but the term ‘sustainability’ has taken on a different meaning over the years. For many, sustainability is about purely environmental matters, but to us, being sustainable means doing the right thing in the world we live in and how we operate as a business.
As a 164-year-old family business, this has always been part of the company ethos – from employing local people and supporting the local community, right through to ensuring our product is as responsibly sourced and manufactured as possible.
Proving sustainable procurement was something our former chair and MD, Neil Donaldson was championing before any certification schemes were established. As soon as chain of custody and sustainable sourcing were available, we were one of the first timber businesses to achieve and maintain FSC and PEFC certification. Sustainability has never just been a box-ticking exercise.
Jump forward to 2024, and ‘sustainability’ in an environmental sense, has never been more important. In true Donaldson style, when considering our own environmental impact, we aimed high and promised to do good – in environmental terms, this means Net Zero. To achieve this, we need to more meaningfully reduce value chain emissions; looking beyond what we do as a business and considering what our customers and suppliers do too.
As part of this process, we established our carbon footprint to ISO 14064 (carbon footprint verification) and discovered that only 3% of our carbon footprint is generated by the Group. 97% of carbon is generated by suppliers and customers.
This led us to look at the whole life carbon of our products, and the often overlooked (and trickier!) area of embodied carbon. These are the cradle to grave emissions, including: growing the core material, transportation, the addition of our own carbon footprint through manufacture, delivery to our clients, end of life and how we dispose of it.
We know that our customers are looking to meet targets, and they need proof of environmental claims to do so. Our work on achieving ISO 14064 and our goal to meet the changing needs of our clients, resulted in a project on Environmental Product Declarations (EPDs). These are key to proving and achieving zero carbon, as they give the lifecycle of a product through third-party verified data.
We believe that our products are the sustainable choice for our customers, but these days, claims are not enough. To support the customer transition to Net Zero and provide them with the information they need, we started a project to achieve EPDs for our flagship products across the Group. In this time, we’ve seen an increase in demand for EPDs, as more businesses look to become Net Zero and meet government targets.
EPDs are a big investment, but they’re worthwhile. We’re proud to have completed seven EPDs in the last 12 months, showcasing the sustainability credentials of a fantastic array of products, from Perform Panel’s laminated wet wall panels to James Donaldson Timber’s European Redwood.
Our offsite frame manufacture business, Donaldson Timber Systems (DTS) became the first timber frame manufacturer to offer an independent, accredited environmental product declaration (EPD) for an off-site assembled timber frame wall panel. This is key evidence for sustainable housebuilding and meeting Government targets.
Our goal as a group is to become a leading independent net zero carbon business. We want to provide solutions that help our customers to be carbon neutral; we want to ensure a sustainable supply chain, and crucially, we want to guarantee that all parts of our business can back up any environmental claims.
The next task is how we target improvements over the next 20 years to fully achieve carbon net zero. We have plans in place to generate our own electricity – solar panels have been installed at five of our sites over the last 10 months – and we’re already seeing the benefit from this. When we add this to our ISO 50001 certification which helps to manage our energy use, these strategic initiatives mean when we come to undertake our EPD assessments in five years’ time, the results will be even better.
Nobody knows what the next 20 years have in store, but we’ll continue to do good – leading the way in sustainable business approaches.