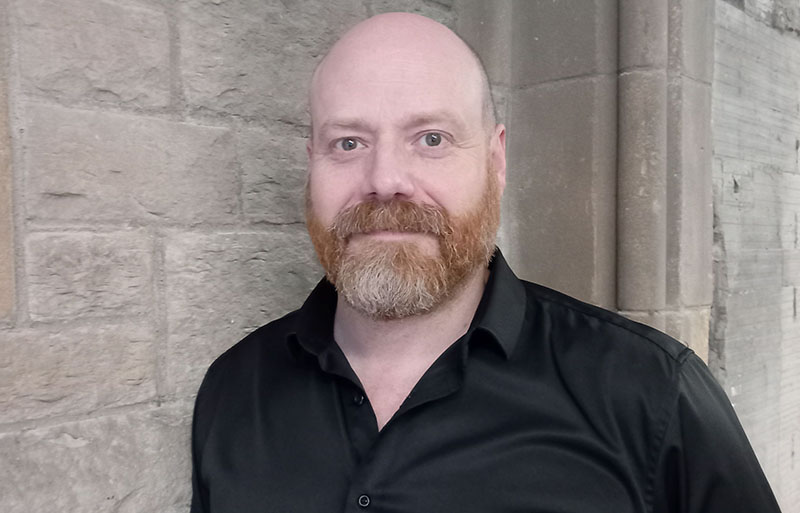
By Rob Bewick, senior construction safety consultant at Thomas & Adamson, part of Egis Group
The latest Health and Safety Executive (HSE) statistics on work-related fatal injuries don’t paint a great picture for construction. Yet again the sector saw the highest number of fatal injuries by sector, with 51 for 2023/24 – more than double the 23 recorded in the agriculture, forestry, and fishing industry, the next highest industry.
Worryingly, the number of fatalities in construction rose last year from 47. That figure was also significantly higher than the five-year average of 42 and was a statistically significant amount above pre-pandemic numbers according to the HSE.
The bottom line is that no one should go to work and be at risk of not returning home later that day. While construction is, by its nature, a more dangerous environment than many others, there are tried and tested ways of managing those risks to protect workers while they are on site.
Falls from height were the leading cause of fatal accidents across all sectors, at 50 – double the 25 cases of workers being struck by moving vehicles. Being hit by moving objects and being trapped by something overturning or collapsing accounted for another 20 and 15 fatal accidents, respectively. All of these are possible on a building site, but, more importantly, they are also all preventable.
Preparation is a crucial part of prevention – and, for the construction sector, two documents required under the CDM regulation 2015 lay the foundations of good health and safety management throughout the duration of a project. Importantly, no work on site should begin without them being shared with the relevant people involved.
The first is a Pre-Construction Information Pack (PCIP) prepared by the Principal Designer. The PCIP should contain all information that is ‘reasonably obtainable’ related to the planning and management of the project, including potential health and safety issues from a design and construction perspective, along with how these will be addressed.
The PCIP must be concise and easily understandable for everyone who will use it, as well as clear in its language and presentation. Appointing a Principal Designer early in the pre-construction phase will allow them to work with the developer from the off, setting out a clear plan to minimise risk at every stage of the project and, ideally, design out likely issues – for example, by using equipment or technology to replace the need for people to work at height.
Secondly is the Construction Health and Safety Phase Plan (CHSPP or CPP). This document is developed by the Principal Contractor from the information supplied in the PCIP. It should detail the safety control measures implemented for the duration of the construction phase to ensure the hazards identified in the PCIP have been addressed and should be communicated with everyone working on the site to ensure they are aware of their responsibilities, safety controls, and site rules.
Good health and safety practice doesn’t end with the creation and distribution of a couple of documents. They need to be easily available to everyone on site at each phase of the project and checks should be made that what is actually happening on the ground reflects what was put on paper.
Above all, everyone working on site should be health and safety trained to a high standard, so that they understand any potential hazards and how to prevent them. Daily walk around inspections is another straightforward exercise, making sure everyone is aware of their environment, the hazards within it and associated risks, and that they have a responsibility to maintain safety standards.
A regular series of ‘toolbox talks’ are also highly advisable – and there are helpful templates you can download from the HSE website as well asother sources. It can also be a good idea to ensure the construction programme is easily available on site so that everyone can see what work is taking place at different stages, when and where machinery is being used, and any areas that will be exclusion zones.
Huge amounts of effort are put into keeping people safe on site – but all of that can come undone if the right information hasn’t been shared with the right people at the right time. PCIPs and CPPs are the bedrock of a making sure that happens, ensuring they are created, shared, and implemented in the best possible way to keep people safe and, ultimately, help the industry reverse the current trend in on-site fatalities.