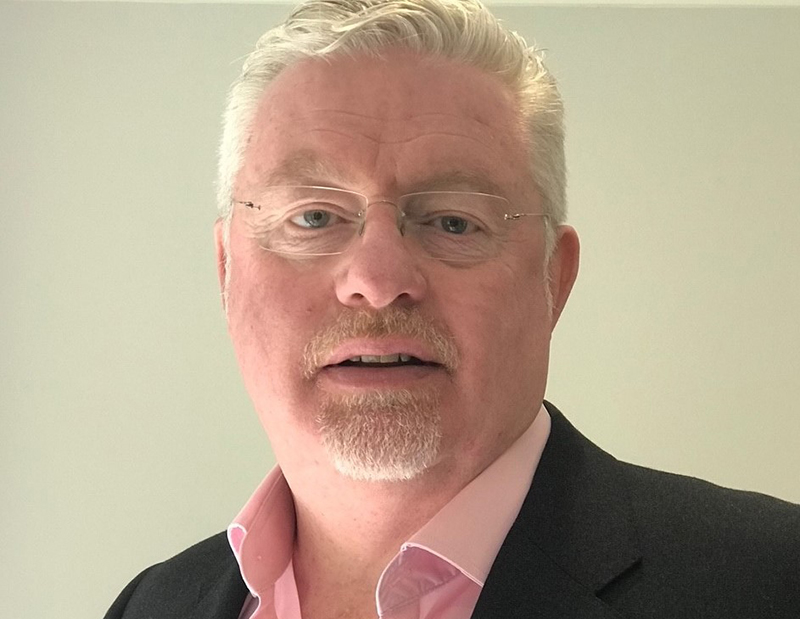
By Mike Stevenson, senior manager strategic markets at NorDan UK
IN April, Homes for Scotland (HFS) called on the Scottish Government to ‘pause and review’ any further legislation towards reducing carbon emissions in the housing sector, including the Scottish equivalent to the Passivhaus Standard for new homes due to be implemented by the end of the year.
Responding to the Scottish Government’s admission that it could not meet its commitment to a 75% reduction in carbon emissions by 2030, the HFS called upon it to ‘work with us and other stakeholders to prepare a clear road map which would enable the sector to deliver low-carbon homes at scale and pace’.
While the industry body says it has been ‘clear and consistent’ in its support of the need to reduce carbon, it believes imposing regulatory demands on developers now could hamper their ability to build the number of homes needed to address the current housing shortage in Scotland.
In my view these two challenges, reducing carbon and building more homes, are not mutually exclusive. I would even say that the proposed Scottish Equivalent looks like it will not include the measurement and reduction of embodied carbon. This is the carbon generated from the building products specified and the construction process.
Embodied carbon is the elephant in the room, and ignoring it risks skewing the debate around decarbonising housing to one of costs rather than value and sustainability.
Currently there is too much focus on capital cost instead of whole life cost when building new homes or refurbishing existing ones. This usually results in decisions like the use of PVC windows because they are seen as being cheaper than high-performance alternatives, which are normally constructed from aluminium clad timber.
Even when architects specify high-performance windows, plans often undergo ‘value-engineering’ with timber windows being replaced by plastic in the specification.
This is short-sighted and more costly, both financially and environmentally. Much more carbon is emitted during the production of PVC windows, and because they do not last as long as high-performance aluclad timber units, they will need to be replaced and disposed of more frequently during the 60-year design life of the building. This creates a significant whole life embodied carbon footprint.
Because windows and doors are responsible for 20% of a home’s total heat loss, installing PVC windows can result in higher operational carbon output as well. This means homes that are more expensive to heat for residents, many of whom already face fuel poverty.
At a time when the biggest challenges facing Scotland are the cost-of-living crisis, the housing crisis, and a climate emergency, rejecting measures such as the Scottish Equivalent seems counter-intuitive. Especially when there are examples of existing developments reducing embodied and operational carbon, while also making financial sense.
Take Prospecthill Court, a 16-storey residential tower block in Greenock, owned by housing association River Clyde Homes. As part of a £4 million regeneration and retrofit programme, River Clyde Homes chose an external cladding option that, while not the cheapest, will provide lower whole life cost, including reducing carbon by 3,500% and helping to significantly lower fuel bills for residents.
As part of the project, River Clyde Homes also installed almost 340 NorDan UK StormGuard windows because they met its performance specifications and philosophy. StormGuard’s aluminium-clad timber design come with a 60-year life expectancy and reduce heat loss, which reduces carbon emissions and helps to lower energy bills by keeping homes warmer.
Because of the way they are manufactured, including being largely made of timber, StormGuard windows have low embodied carbon. NorDan UK measures this with our unique Dynamic EPDs (Environmental Product Declarations), which generate data on embodied carbon across all the windows on a project. It is information like this that helped River Clyde Homes choose NorDan UK.
Prospecthill Court is an exemplar of how all the pressures on housing can be balanced, from reducing whole life carbon to ensuring good value. So it is not surprising that so many architects and specifiers are visiting the development to see what River Clyde Homes is looking to achieve.
This was all done ahead of the introduction of new regulations, so it demonstrates that the expertise and willingness to decarbonise our homes, while also considering financial challenges, already exists.
We just need to be better at sharing this knowledge and working together as a sector.
I am not alone in thinking this. Richard Orr, head of asset and regeneration at River Clyde Homes, is an advocate for collaboration between landlords and the supply chain. As Richard puts it: “The impending climate emergency means we have a moral obligation to assist each other in answering key questions and providing access to information. This includes sharing critical knowledge on specification, how we finance change, and the kinds of conversations we need to have with our boards to enable us to set our own low-carbon design parameters.”
I echo Richard’s view that the sector should collaborate to scope out the scale of work and resources needed, and how best to deliver it. “If we do not,” Richard says, “we will continue to see hundreds of individual housing providers all competing for the same finite volume of products later in the purchasing cycle.”
So in this sense Richard and I agree with the HFS’s view that the housing sector should work together. But I believe this collaboration should happen as part of a process that includes a compelling regulatory framework, rather than instead of it.
This will ensure that we all remain focused on the vital goal of creating more high-quality, low-carbon, cost-effective and sustainable homes for the people of Scotland.