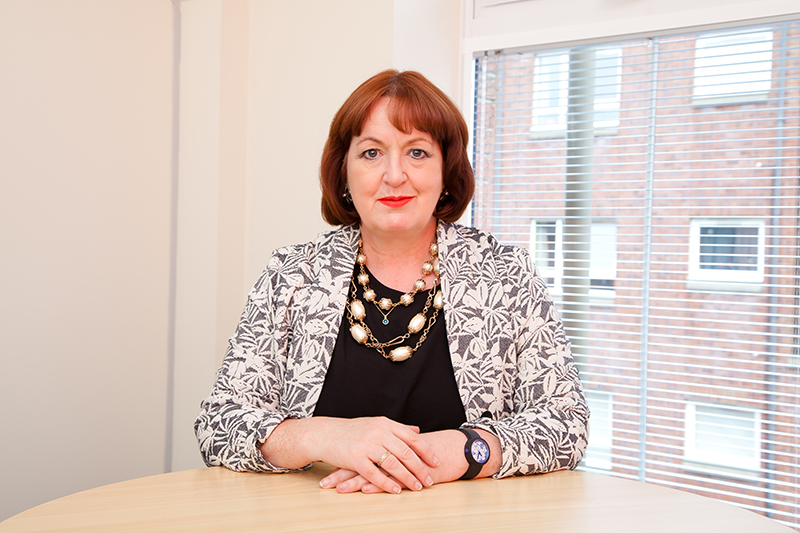
Following the news that hundreds of residents in Aberdeen’s Balnagask area are to be relocated after RAAC panels were found in around 500 homes, including 364 council properties, Lesley McLeod, chief executive of The Association for Project Safety (APS), tells Project Scotland why the construction industry needs to learn the lesson that specifying cheap material comes at a cost
WHEN people lived in mud huts or simple shelters the worst that would happen if the roof caved in was a few scratches and a night in the cold and wet. Today the stakes are much higher. With the need to build affordable new homes – as well as renewing our ageing schools, hospitals, and transport infrastructure – the UK construction sector needs to look to innovative techniques and products to get the job done.
But we also need to take heed of those echoes from our past before the first spade goes into the ground. Recent experiences from the complications of using RAAC have lessons for us all.
Reinforced Autoclaved Aerated Concrete was once seen as a bit of a miracle product. It was lighter than traditional materials, so it went up fast and was easy to handle. It made projects flexible because walls could go up without the need for extensive footings and complicated engineering and underpinning. And, at a time when new public buildings were urgently needed, it was – with the country facing tough financial times – cheap. Or, at least, cheaper than many of the alternatives.
But, like your granny may have cautioned you when choosing anything from new shoes to furniture, it is often a case of buying cheap and paying dear. At so it has proved with RAAC. Nor has it been the first time. Other wonder-products have had problems too: schools closed because of high alumina cement; and thaumasite affecting motorways bridges.
Putting issues right has been costly. And disruptive.
And now we are seeing schools, hospital wards and even theatres closed as well as people moved out of their homes with little or no warning. It remains unclear how and when problems will be put right. Or who will foot the bill.
When people look to the country’s immediate need for new buildings of all sorts there’s a natural focus on when improvements will be delivered. All governments have placed a great deal of emphasis on speeding up the planning process to ensure there are no unnecessary delays.
Conscious of the urban brutality of tower blocks and office buildings thrown up in the post-war years, there is also a drive to ensure construction is life-affirming rather than something that sucks all joy and beauty out of our built environment.
Certainly, particularly with public projects, there’s a need to scrutinise every penny of public money spent. And a huge amount of criticism heaped on any politician or public figure who oversees soaring costs.
But the trio of planning, pleasure and price risks drowning out the need for safety first.
It will not surprise you that the Association for Project Safety believes safety must be at the heart of everything we build. But design risk management also makes sound sense. It will always be better to get things right first time than having to fork out for the costs of failure.
And that’ll also see more people able to sleep soundly in their beds at night.