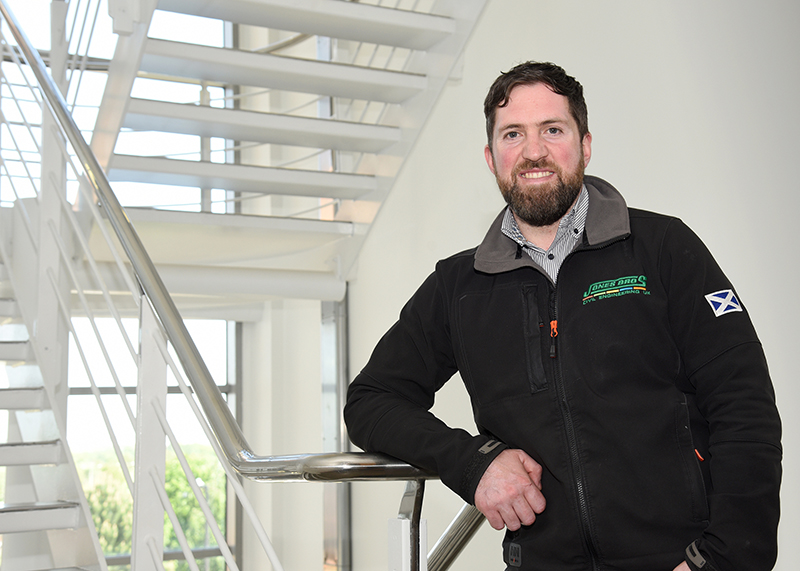
A business decision made by Jones Bros Civil Engineering UK upon its founding in the 1950s is helping the company overcome current-day global issues that are blighting the construction sector, the firm’s contracts manager has told Project Scotland.
The civil engineering contractor, which has a base in Bellshill, North Lanarkshire, made the decision to have all its plant machinery in-house from the outset.
The company’s growth over the years has meant that it now owns one of the largest single plant fleets in the UK, with over 500 individual pieces of kit to call upon.
Such an inventory played a key role in the firm’s ability to pick up Evolving Energies’ (ERG) half-built Sandy Knowe Wind Farm in Dumfries and Galloway and deliver it to schedule, after the previous contractor entered administration just as phase 1 of the project was completed.
The work involved Jones Bros installing a fabricated bridge, as well as creating new access roads and building a crane pad. The business then dug foundations out before installing ten turbine foundations with reinforced concrete foundations, with excavating and backfilling for cabling works then undertaken and the construction of a new bridge across Polneul Burn.
ERG hailed Jones Bros as a ‘reactive’ and ‘proactive’ company on the back of the work, saying that the organisation’s understanding of the situation and project needs played a key role in delivering the development on time and to the required quality, despite tight deadlines.
“If we need to progress a project faster or we’re looking to make the best of a weather window, then we have the ability to do that with our plant fleet,” David Nicolson told Project Scotland, before explaining the flexibility that is achieved by sharing plant with the Welsh arm of the business.
“If we’re experiencing a really bad winter, where not a lot of work can be done, we can up resource things when better weather comes and push things on. That can be done fairly seamlessly, with whatever is needed being brought in.”
David continued, “The company is definitely built on very solid foundations which has allowed us to look at projects that maybe other companies haven’t been able to. The programmes are tight and having that ability to resource fully in-house definitely takes a lot of pressure off. We’re going into fairly high-pressure environments with tight deadlines; if you then add in the issue of resourcing that plant and labour, it would clearly make things a lot more difficult. So, I feel as if we do have a definitive advantage.”
Describing the firm’s build of Solwaybank Wind Farm, also in Dumfriesshire, as a personal career highlight, David told how Jones Bros again utilised its flexibility after the turbine supplier went into administration at the project’s halfway point. Jones Bros had to change the design of the foundations to accommodate a new turbine type, as well as battling against ‘significant depths’ of peat up to four metres.
It isn’t just the plant fleet that is helping Jones Bros to complete such projects. The company is currently nearing completion of a wind farm build in Benbrack, Dumfries & Galloway, which is being led by project manager Jonathan Maitland. Jonathan joined the firm as an apprentice before working his way up the ranks. Many of his team of engineers on this project recently completed their apprenticeship programme. In total, 40% of Jones Bros’ 500-strong workforce began as apprentices – including some current directors.
“The apprenticeship programme is brilliant,” David stated. “It offers a path from apprentice to director. The company wants people to progress to higher up and if someone wants to get to a director position, that door is open. There’s no barrier there, just progression routes.”
Jones Bros offers apprenticeships in the company’s key focused areas of energy and renewables; flood and coastal infrastructure; waste management infrastructure; private developments; highways; and quarrying. David explained that, like the plant fleet, the pool of talent means a wide range of resources can be called upon.
“We’re a close company with a good culture across the board,” he explained. “We’ve also got a lot of staff that we can bring up a level, and if we’ve got a shortfall at a slightly lower level, we know the guys will step down to cover a certain role if they need to.”