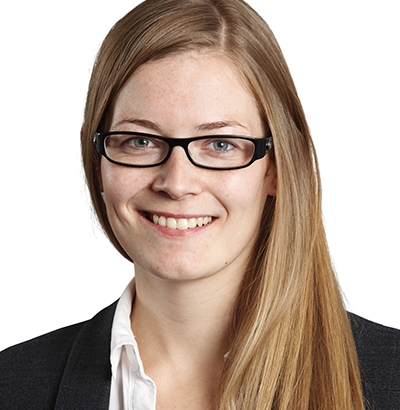
Linzi Hedalen, partner at Dentons, discusses risk management and proactive strategies to avoid the effects of supply chain disruption
THE construction industry has not had an easy time in recent years: contending with the fallout from Brexit; the lockdowns arising from the Covid-19 pandemic; the shortages in labour and materials; the resulting price hikes and spiking inflation rates. We are still in the midst of the Ukraine war and now have new leadership and new agendas in both the Scottish and UK governments.
It is therefore not surprising that, given all of these factors, insolvency numbers are rising in the industry. Albeit there are green shoots and talks of recovery, it is foreseeable that more disruption will arrive in the form of ESG, extreme weather events, technology and further regulation. Â
It is, therefore, important to consider what can be done by employers, contractors and suppliers to iron out any kinks in the supply chain, mitigate risks and ensure the survival of the industry.
In the beginning
Before putting pen to paper when contracting for a project, due diligence is key. Parties should know their supply chain and its capabilities. Tried and tested firms may be safer to appoint than a new-start with no track record. Employers may want to retain control of the subcontractor appointments to ensure there are no weak links.
Both parties should ensure that they are aware of any vulnerabilities in the supply chain, which can be monitored either through the contract terms or by ongoing due diligence.
Contractual safeguards
Once the supply chain is in place, the primary form of defence against disruption is a comprehensive contract that protects parties from the unforeseeable and unexpected.
Albeit parties will have competing interests when negotiating terms, a properly considered contract can provide protection for both parties and may consider the following provisions/doctrines:
• Price fluctuation provisions – these can help to alleviate the financial pressures that have, historically, been placed on the contractor, possibly protecting them from insolvency and, consequently, protecting the project and the employer’s interests. Such provisions can be drafted to have caps, but can also allow for the employer to share in any gains from efficiencies.
• Advance payment for materials – this may allow contractors to achieve better prices and reduce costs. However, there should be consideration around ownership of such materials in advance of incorporation on site.
• Employers may stipulate periodic written confirmation from its contractors that subcontractors and/or suppliers have been paid to ensure arrears are not building up.
• Force majeure provisions – contracts can contain force majeure provisions which allow claims for an extension of time and/or price adjustment when an event causing delay to completion occurs, but which was not reasonably contemplated by the parties when the contract was entered into. Events known to the parties will unlikely fall into this category.
• Termination provisions – parties should be aware of the termination provisions. Often employers will seek to have the option to terminate at will or in the event of insolvency. Contractors should ensure the provision for damages will be sufficient should they accept such drafting.
• Frustration – frustration of a contract occurs when it becomes impossible to carry out the terms of the contract. Given the current sanctions and restrictions due to the Ukraine war, this doctrine may be relevant. The fact that a project becomes more expensive is not, by itself, a reason to operate the doctrine. Seek legal advice before operating this principle as wrongful termination will likely result in liability for damages.
Insolvency safeguarding
Having an iron-clad contract is one thing but, if a party is inevitably heading towards insolvency, it is important to be alert. Behavioural changes are a key indicator of hardship and can include: payment applications turning up out of sync; site visits being cancelled; delays in payment; or a lack of activity on site. If anything appears out of the ordinary, you should take a closer look.
Regular checks of the Edinburgh and London Gazettes and Companies House filings should be carried out. Late filings of annual accounts can be a telling sign.
If you are faced with a possible insolvency in the supply chain, preparation is key. An employer should ensure a full suite of collateral warranties from sub-contractors and dust off any performance bonds. Further, the non-affected party should ensure it is complying with the terms of the contract including issuing notices timeously, in the correct form and by the stated method. They should not react on the predication that insolvency is looming. Such action may result in a repudiatory breach.
Conclusion
Supply chain disruption is a subject that is here to stay for the foreseeable future. It should be taken into account when identifying opportunities, negotiating contracts and managing live projects. The effects can strike at any time. Accordingly, parties should proactively manage the risks by making smart choices; engaging with all parties; and ensuring that protections are in place.