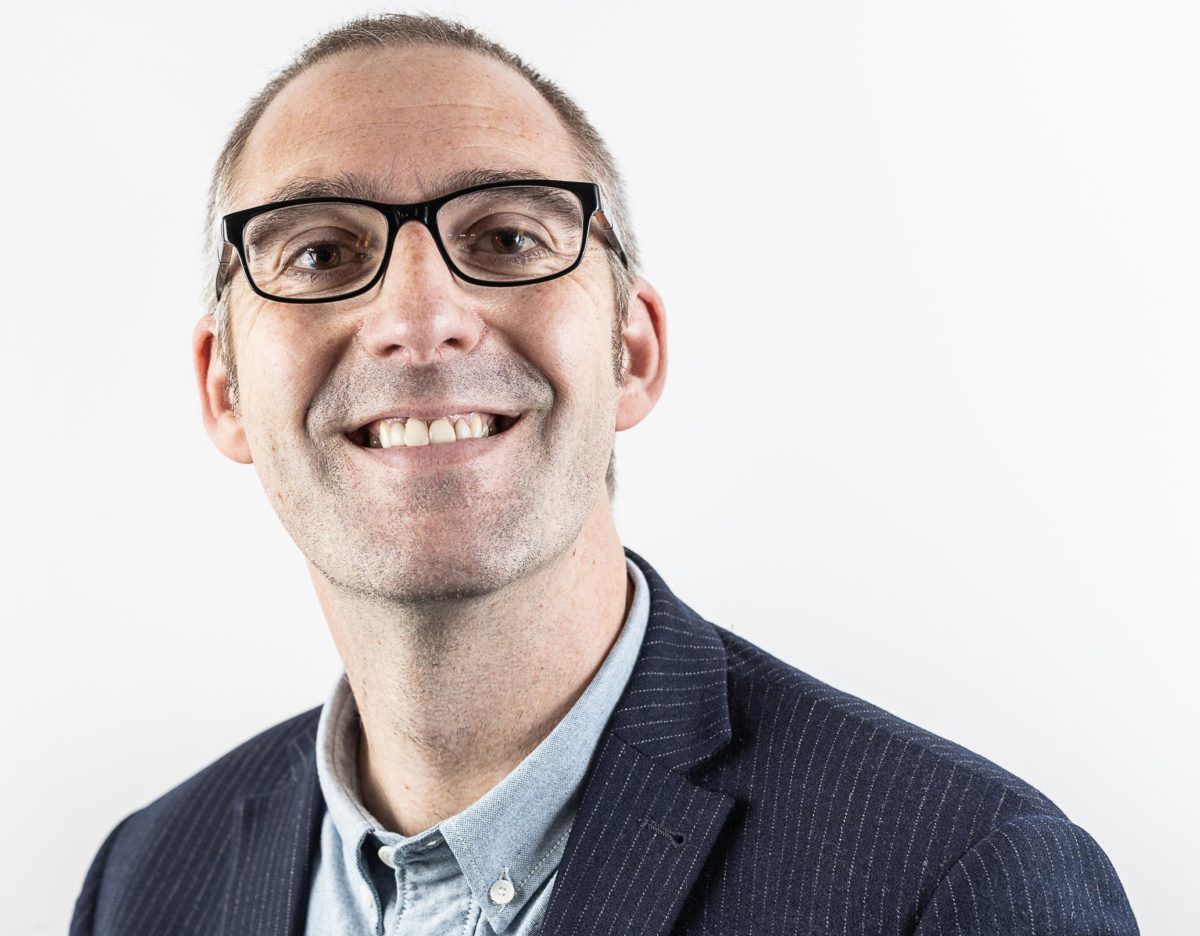
By Stuart Fleming, director, Will Rudd
PROPERTY owners and managers of buildings built between the mid 1950s and early 1990s will be interested to know that the Local Government Association is advising its members to check as a matter of urgency whether any buildings in their estates have roofs, floors, cladding or walls made of Reinforced Autoclaved Aerated Concrete (RAAC).
At Will Rudd, we are increasingly involved in helping many of our public sector and private clients manage issues relating to the building material RAAC within their properties.
Some readers will be familiar RAAC under various brand trade names.
What is RAAC?
CROSS UK describes RAAC (Reinforced Autoclaved Air-Entrained Concrete) as a lightweight form of concrete used in roof, floor, cladding and wall construction in the UK from the mid-1950s to the mid-1980.
Autoclaved aerated concrete (AAC) is different from normal dense concrete. It has no coarse aggregate, and is made in factories using fine aggregate, chemicals to create gas bubbles, and heat to cure the compound.
CROSS UK identifies that when reinforced (RAAC) is used to form structural units, the protection of the reinforcement against corrosion is provided by a bituminous or a cement latex coating. This is applied to the reinforcement prior to casting the planks. The reinforcement mesh is then introduced into the formwork and the liquid AAC mix added.
RAAC panels were specified primarily in offices and schools, but RAAC has been found in a wide range of buildings, not all of which are still in the public sector.
What are the issues?
RAAC is relatively weak with a low capacity for developing a bond with embedded reinforcement.
The limited durability of RAAC roofs and other RAAC structures has long been recognised; however recent experience (which includes two roof failures with little or no warning) suggests the problem may be more serious than previously appreciated and that many building owners are not aware that it is present in their property.
In the 1990s and again in 2002, the Building Research Establishment described the difficulties in service with RAAC roof planks and commented on cases of excessive and progressive deflections in service, associated with widespread hairline cracking of the soffit of the planks. It is therefore essential to reconsider maintenance and inspection regimes.
Following previous tests carried out by the Building Research Establishment, it was thought that RAAC planks gave adequate warning through visual deterioration before failing. However, the two recent failures occurring with little or no warning show this can no longer be relied upon. (Cross Safety UK).
What you need to do
- Ensure that the condition of all your buildings is regularly monitored, taking a risk-based approach that gives due deliberation to the use of the building with consideration given to the possible impact of reduced maintenance.
- Ensure you have identified any RAAC property in their portfolio.
- Ensure that RAAC properties are regularly inspected by a structural engineer including using a cover meter to check the provision of traverse and longitudinal reinforcement, note deflections, check the panels in the vicinity of the support, the width of the support bearing, cracking, water penetration and signs of reinforcement corrosion and any inconsistencies between panels. The frequency of subsequent inspections should be determined by the structural engineer conducting the initial inspection.
Adopt good roof maintenance practices as follows:
- Ensure water outlets are clear and are at such a level that allows free drainage of water from roof areas.
- If the internal surface of the planks is to be decorated, use paint which allows moisture vapour to pass through it. Protect external surfaces with a coating which provides an effective barrier against the transmission of liquid water.
- Where appropriate, reduce the dead load on roofs by removing chippings and replacing them with an appropriate solar reflecting coating.
- Ensure that all waterproof membranes are maintained in good condition.
- Keep records of deflections of RAAC planks and inspect the construction regularly.
Ensure that those responsible for the day-to-day management of any RAAC building:
- Know that RAAC is used in the building and where it is used.
- Check regularly for visual signs of cracks, water penetration, deflection to soffits and ponding to roofs.
- Ensure that all staff know to report any cracks and or other identified potential defect issues.
- Are instructed to immediately close off any part of the building where cracks or other material defects appear pending further checks.
We can help
Structural engineers such as Will Rudd can guide you and lead a process of interrogation and investigation of the RAAC elements with regards to establishing its structural safety. Typically, such a process would include:
· Visual inspections, measured surveys and intrusive investigations can inform a risk-based assessment to establish whether there is any heightened risk of failure.
· Cover meter tests to check the provision of traverse and longitudinal reinforcement; surveying to establish magnitude of deflections; checking the panels in the vicinity of the support; the width of the support bearing; visible cracking; water penetration and signs of reinforcement corrosion and any inconsistencies between panels.
· Recommendations for the ongoing management and maintenance of RAAC structures, provide ongoing and periodic support to ensure that the remaining life of the structure is understood, and the ultimate replacement of the RAAC can be suitably planned for.