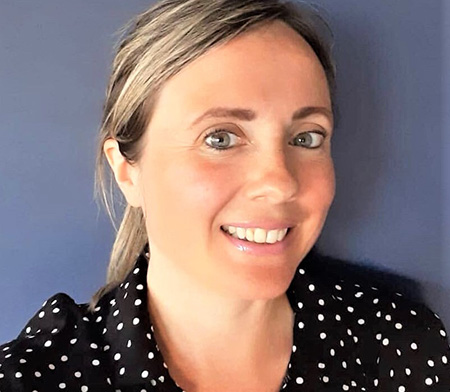
By Ellen Delph, project manager, KR Group (Scotland)
THE days of us living our lives within, what might be termed a linear production model – in other words, we extract, produce, consume, and discard – are now viewed as a significant concern for the planet.
According to Zero Waste Scotland, around four fifths of Scotland’s carbon footprint come from the products and materials we manufacture, use, and throw away. Indeed, from the research we have carried out, we can prevent around 7,736 tonnes of carbon emissions within the next five years, which will help supercharge the industry within which we operate, namely building construction on a journey towards a net zero future.
When our cladding division was established in 2017, one of the problems we faced was disposing of old PIR cladding panels removed from buildings. These would normally be destined for landfill, because there was no reuse option for these older panels.
Our ethos is very clear. No more cladding materials to landfill!
To help achieve this, our specially created circular economy division, KR Bon Reduction will process some 2,653 tonnes of cladding waste – mainly waste composite PIR (Polyisocyanurate) cladding panels over that period. Extensive R+D, part funded by Zero Waste Scotland and European Regional Development Fund (ERDF), has enabled us to repurpose and re-energise this PIR as an innovative rigid insulation for use in construction industry.
Much of what we are now doing is helping to address some of the concerns raised by CeeD (Centre for Engineering Education and Development), which champions Scotland’s manufacturing sector. It raised concerns that one of the biggest barriers to scaling the circular economy is maintaining visibility and control over manufactured materials when they enter the waste system – a particular focus for CeeD, as they are working with Topolytics on their WasteMap project to help improve energy efficiency, productivity, and the sustainability of manufacturing processes.
We commissioned an independent report in 2019 carried out by Ricardo – the global strategic engineering and environmental consultancy. It examined the potential re-purpose and reuse options, which identified possible Co2 savings generated by reusing the material.
The report concluded that the best reuse option was to keep the PIR Panels as whole units. They retained good thermal properties as insulation boards however, further tests were needed. The aftermath of the Grenfell Tower fire raised questions about the efficacy of the external cladding panels, so all cladding materials would normally need to undergo a series of fire tests.
We received validation from environmental regulator SEPA that the business can repurpose the waste cladding material.
PIR is discarded into regular waste skips and unmeasured. Our data determined that from the present onwards we will see buildings being deconstructed because these panels only have a warranty period of between 15 and 25 years.
However, we can only repurpose panels from 2004 onwards, because anything before that date has ozone-depleting substances (ODS) within them – so as they are cut, ODS are released into the atmosphere and that cannot be allowed to happen, so collecting PIR Boards from 2004 onwards has become our benchmark and anything post 2019 we’re likely to see buildings being deconstructed and fitted with new cladding materials.
These benefits in salvaging cladding waste are quite profound.
• 7,736 tonnes of CO2 (equivalent) prevented—the equivalent of removing 4,460 cars from UK roads
• 675 new homes could be insulated with an estimated cost saving of up to £1.88 million pounds
• 2,498 tonnes of waste diverted from landfill—the equivalent of 8 Olympic swimming pools
This is why we need to continue this net zero journey. The building and construction industry need to be ‘hard-line’ in their actions. It’s imperative that they start to find value in their waste and find solutions on how it can be repurposed. Ignoring it will continue to harm the planet for future generations.