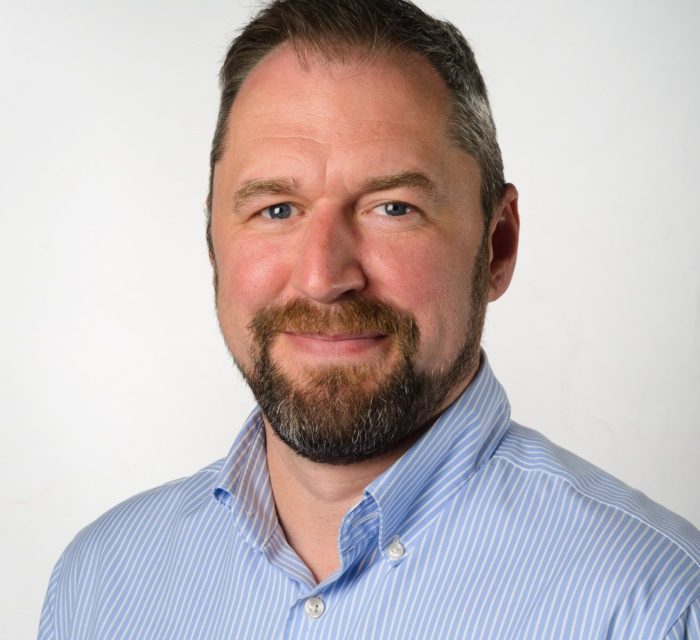
Conventional handset brickwork remains a popular method of protecting buildings in Scotland. If this method was a new solution, however, architects and contractors wouldn’t give it a second’s thought. That’s the view of Grant Softley, technical sales manager of Aquarian Cladding Systems.
THE scariest phrase in the English language is ‘because that’s the way we’ve always done it’ and it’s one that I hear regularly from architects and contractors in Scotland when it comes to the reason why traditional masonry is the preferred method instead of a brick slip system.
Living in Scotland and with more than 10 years in the brick industry, it’s a thought process that I am more than familiar with. And while brick façade systems are gaining in popularity in England, as an alternative in Scotland they are practically non-existent, with decision makers believing they are untried, untested, and therefore risky.
Of course, moving from traditional methods to newer, more modern solutions can seem like a leap into the unknown – whatever the advantages.
But what if brick cladding was the traditional method that had been around for hundreds of years, and traditional masonry was the new, innovative system? Would architects and contractors think it was the best way forward? I very much doubt it.
Slower, more materials and labour intensive
If I was to sit in front of an architect or contractor and introduce traditional masonry as the new innovative idea instead of using brick façade systems, and said it was a method that required them to bond individual bricks together one at a time using more mortar and an increased labour force, they’d probably show little interest.
If I then revealed it would mean an increase in the build programme, an increase in delivery vehicles by 75%, it would mean having to introduce scaffolding and mortar silos not to mention an abundance of masonry support. They would also require a weather dependent work force to be drawn from a scarce skill pool. Its feasibility would be questioned.
So, in this scenario, as an architect or contractor, why would they opt for handset brickwork over a system that offers a quick, simple, and predictable, robust solution with fewer design and construction limitations?
Saving money
Cost is, of course, a huge consideration and, while side-by-side brick cladding materials are more expensive than bricks and mortar. The conversation rarely moves past this stage in Scotland, when in reality the reduction in cost of the overall project is considerable.
The system can be manufactured offsite, saving money on labour, prelim costs are reduced, with no need for scaffolding or masonry support. It can takes weeks off your build program, with greater flexibility of build sequencing resulting in minimal delays, all contributing to greater cost efficiency.
We used to build houses out of mud so building products have continuously improved and if we had continued to use traditional methods ‘because it’s the way we’ve always done it’ when bricks came into fashion then where would we be now?
Change is the only way industries continuously improve, and with architects and contractors under increasing pressure to reduce construction costs and build-time, brick slip systems must be given serious consideration.