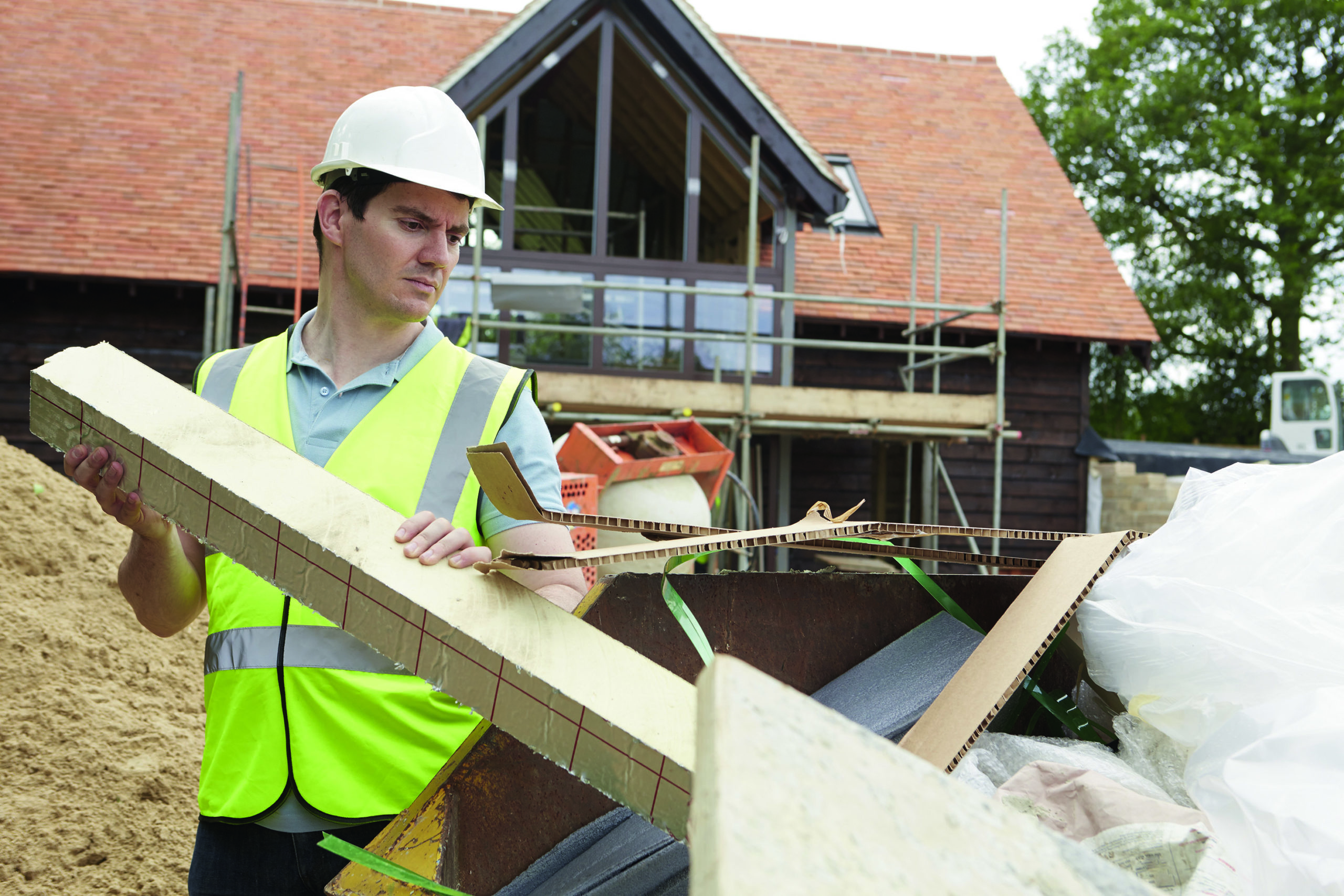
A former site manager turned university professor has warned construction firms could face ‘turmoil’ in the near future unless they start thinking more carefully about the management of waste.
Professor Billy Hare, deputy director of Glasgow Caledonian University’s BEAM Research Centre, told Project Scotland that impending climate and environmental legislation will hit contractors ‘like a train’ unless they start taking better control of waste immediately.
The academic, who is also part of the university’s school of computing, engineering and built environment, is working alongside colleagues Dr Kenneth Lawani and Siobhan Morison, on a project to determine the true waste costs on sites. The aim is to create an average cost which can be used to predict, and better manage, waste on future builds in the hope of giving firms a better base than the original estimation of £1,300 per tonne of waste.
“The original cost-of-waste figure was based on a simplistic method of calculating it; they took one skip, recorded the contents, and then put a cost against that,” Professor Hare explained. “So, if you purchased the materials that went into the skip that are now obsolete, damaged, or surplus to requirements, then that’s a cost that was calculated. They used a basic hourly rate for labour for the cost of gathering and bringing the waste to the skip across the site, and that was it.”
Professor Hare and his colleagues’ method builds on a trial undertaken by the university prior to the pandemic, with it determining the average site cost to be £1,619. The research examined the root cause of the waste – be it overordering, an attempt to clear space on site, or build errors – to better understand how such disposal of materials can be avoided.
Furthermore, walking travel times are also incorporated into the calculation, as well as the time and electricity and/or fuel used when travelling by a hoist, telehandler, or forklift – all to build a more comprehensive and accurate value of site waste.
The new Zero Waste Scotland-funded pilot will be far more comprehensive, with more firms and projects onboard. Professor Hare revealed that in the original pilot, which involved three firms, one project’s waste came in at over £2,000.
“Projects differ, and that’s because we’re sampling sites of different nature,” Professor Hare added. “The one that was over £2,000 of waste was a housebuilder. This is just a personal opinion, rather than any empirical evidence, but I feel that, perhaps, housebuilders have better margins so they’re maybe just a bit more complacent because of that – but, also, they’re using a lot of subcontractors, and there’s a lot of variations in the materials being used in the build of a house.”
The site in the original pilot study with the least amount of waste cost was a civil engineering groundworks project, where the majority of skip waste came from welfare facilities.
“It was mostly the waste from the cafeteria that was going into the mixed-use waste skip,” Professor Hare said. “So, for different reasons we identified opportunities there to maybe reduce up to 70% of the skip.
“With civil engineering, the difference is that you’re using much of the same material over and over again. You tend to be doing that sort of work in a big open space; you’ve got room to bury inert materials as opposed to putting it in the skip and you’ve got better options – it’s a bit easier to keep the mixed waste down.”
The academic revealed there was a ‘struggle’ to get contractors on board for the initial trial in 2019 despite figures that year showing over a third of the UK’s waste came from construction. However, this time around they have more firms than needed, which is a reflection of a number of factors including more awareness of sustainability issues and the rising costs and shortages of materials.
Professor Hare added that those in the industry who have been shown the trial figures are ‘shocked’, but ‘very few’ act upon them once the initial surprise subsides. He believes this is possibly because, once they crunch the numbers, they conclude that other costs trump those of segregation or paying attention to waste.
“I think that (attitude) is changing and if firms don’t realise that now then it’s going to hit them like a train coming down the road because of what’s coming in the future in terms of CO2 emissions from their waste, other environmental regulation and requirements from clients, net zero ambitions, materials shortages, and the plastic packaging tax.
“The financial argument will possibly not even come into it, because it’ll just be a case of you need to meet the carbon target – therefore you need to do all that’s reasonable and practical to meet that.”
Stephen Boyle, construction manager at Zero Waste Scotland, said, “The construction sector accounts for 50% of the UK’s resource consumption, with embodied and operational carbon from the built environment accounting for 40% of the country’s total emissions. This pilot is a fantastic opportunity to better understand the true cost of waste onsite and the emissions that arise from these.
“Understanding and reducing waste offers opportunities for financial and economic growth at a time when construction costs are increasing and margins decreasing. Driving down Scotland’s consumption of resources will contribute to the ambitious 2045 net zero emissions target set out in Scottish Government policy.”