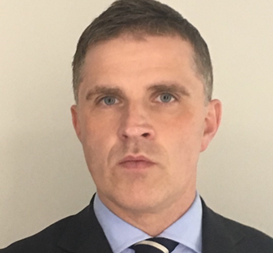
Cameron Gray, cost consultancy director in CBRE’s project management and building consultancy team, explores material shortages and rising costs
THERE has been a lot of concern within the construction industry regarding the availability of materials such as steel, timber and cement-based products. It has had and is having a major impact on programmes due to longer lead times and price volatility.
The shortages are said to be the result of a combination of factors creating what could be classed as a domino effect: Covid-19 delays impacting on the initial manufacturing process, a rush in global demand post lockdown causing supply chain bottlenecks, container shortages and port delays partly due to shipping lanes being incredibly busy and not helped by the Suez canal blockage, increased administration at UK ports affecting imports and exports due to UK EU Trade and Cooperation Agreement; sharp rises in shipping costs and temporary surcharges.
This is then added to a UK economy on the rebound, including large projects such as HS2 which has increased the construction demand and is adding to the drain on resources.
We are seeing the impact of these issues on our current and proposed projects through regular increases in material prices, and construction programmes are lengthening due to longer manufacture, mobilisation and lead in times. Cost uncertainty within tender returns is also a concern as contractors are excluding the risk of future material price increases until a contract is issued. This exposes the client to more risk and uncertainty making the project less appealing as they cannot confirm a final cost or programme.
Recently we’ve had a steel increase of over £20,000 and a major timber company in Sweden (product not available in UK) pulled its price due to huge demand resulting in them putting a halt on new orders. It has cost us £120,000 to go with an alternative timber supplier.
We’re managing all of these issues by building additional time into programmes and through closer examination of critical path elements to assess any potential material implications. Letter of Intents and PCSAs being used to secure longer lead items ahead of actual requirement and we are collaborating more closely with clients and contractors to provide certainty in terms of both programme and cost.
We are also seeing a move away from the more traditional procurement routes to negotiated or two-stage tenders. These procurement methods see a faster tender process turnaround in an attempt to place contracts and orders sooner thus securing material prices quicker. However, we are seeing more tender period extension requests as tendering contractors are spending more time in dialogue with their supply chain to assess offers and availability within the market. That extra time required could see prices increase making it very difficult for project managers and cost consultants to manage client expectations.
Since Brexit has come with its obvious challenges, the Government needs to explore new trade agreements across the globe to try and find the best value or alternatively invest more in manufacturing in the UK. However, this is not a quick fix solution. Other innovative methods of construction and use of alternative materials need to be explored, but who takes the risk of being a test case for this remains to be determined.
We now also have the added element of considering the carbon footprints of the projects we are working on, particularly on net zero carbon developments as materials need to be sourced as close to the site location as reasonably possible.
I do think that this is already leading to a demand for more UK-based construction material manufacturing. The shortage of materials, the volatile pricing and impact on programmes will continue to have a knock on effect on the pricing and delivery of construction projects in the UK which will ultimately find its way to the developer.
If we can deliver more UK manufacturing of construction materials, it may lead to initially higher construction costs against previous European imports, however what UK manufacturing will do is increase certainty of supply and if there is one thing developers and housebuilders like, it is certainty.
As restrictions ease worldwide, it is anticipated that there will be a shift in consumer spending from manufactured goods to services such as eating out, and visiting attractions, which may in turn result in reduced demand and therefore lower shipping and freight costs. However, initially there may be pent up demand for manufactured goods such as new cars, as Covid-19 restrictions ease.