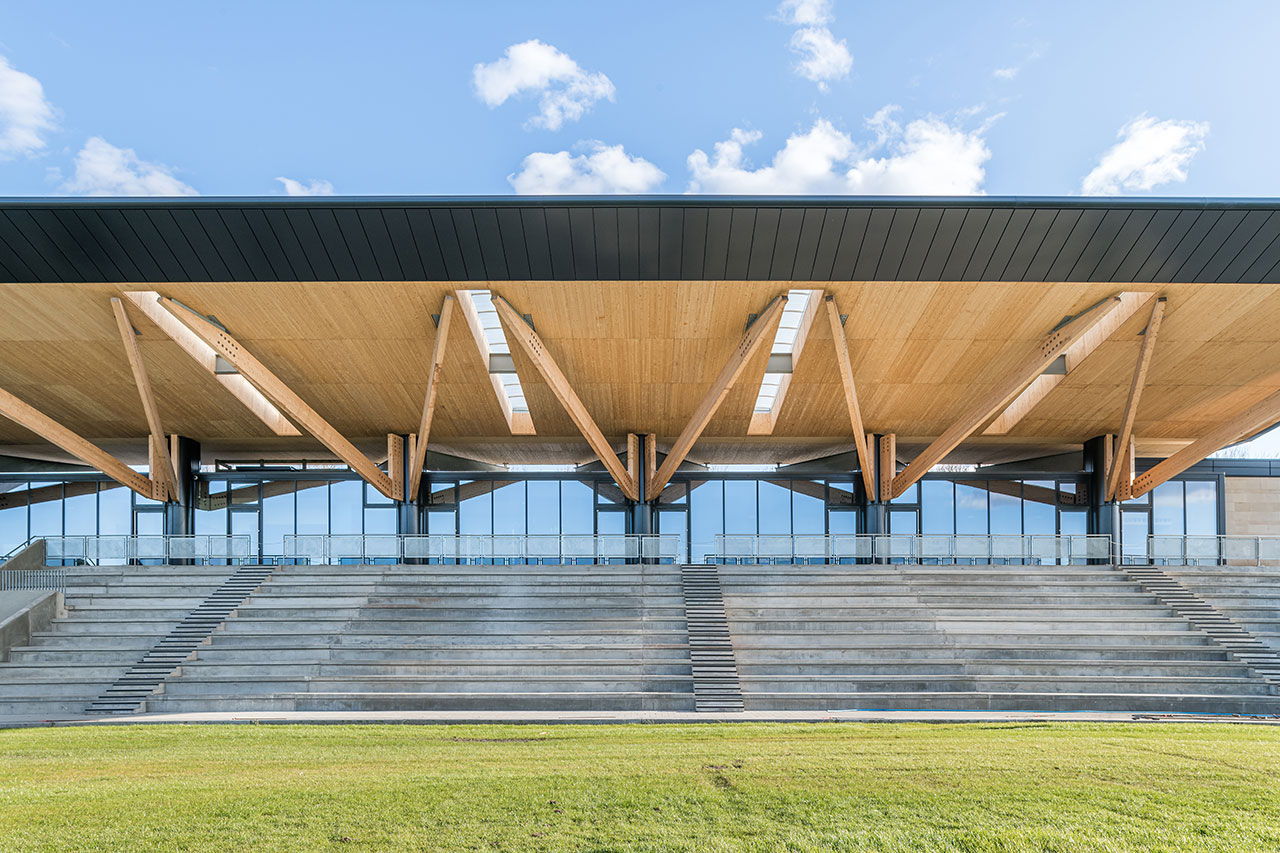
WORKING under the guidance of MLA (Michael Laird Architects), façade specialist MSP recently completed a challenging cladding project for the historic Edinburgh Academical rugby football club. Locally known as ‘The Accies’, the Raeburn Place ground hosted the first Rugby match between Scotland and England in 1871.
The new development will be used by the Accies and other local sporting clubs and includes spectator stands for approximately 2,478 spectators, changing, training and gym facilities, a museum, licensed premises/function rooms and administrative facilities.
While the cantilevered timber structure of the stadium is what first grabs the attention, the development contains a wealth of cladding described as ‘technically challenging and visually arresting’.
Inside the development, curved radius columns create a sense of solidity.
Gillian Thomson, branch manager of Cumbernauld-based MSP Façade Solutions, explained, “The radii of each internal column were not all the same around the face of the curve. This meant that different shapes and profiles were needed for each column to ensure they would fit correctly around the pre-existing steel work.
“Together with our customer R&N Facades Ltd, we were involved at the initial design discussion with the client and developed the original idea before creating a sample design to trial fit on site. The precise dimensions of the samples were then adjusted where necessary to ensure the finished product was a perfect fit. When forming the curves from aluminium sheet, each had to be individually rolled to the exact specification required. So each curve was really made to measure! Once all the design issues were ironed out, each column had to be drawn (using CADCAM), punched, formed and powder coated – all at our premises.”
Outside the stadium, the shopfronts also utilised powder coated aluminium cladding, which was said to be more straightforward. The design comprised goal post style portals using interlocking plank panels in 2mm thick powder coated aluminium.
Gillian Thomson added, “Another surprisingly complex element of the cladding was the external capping. Here, each of the panels and the finished cappings had to be individually drawn in CADCAM, punched, formed and then powder coated to create a seamless, natural look. With natural material such as stone and wood being so important to the stadium design, we had to ensure that all of the cladding – internal and external – maintained this high quality finish.
“Making sure that every joint fitted correctly was vital so our ability to design, model, amend, fabricate and powder coat all the cladding locally was important.”