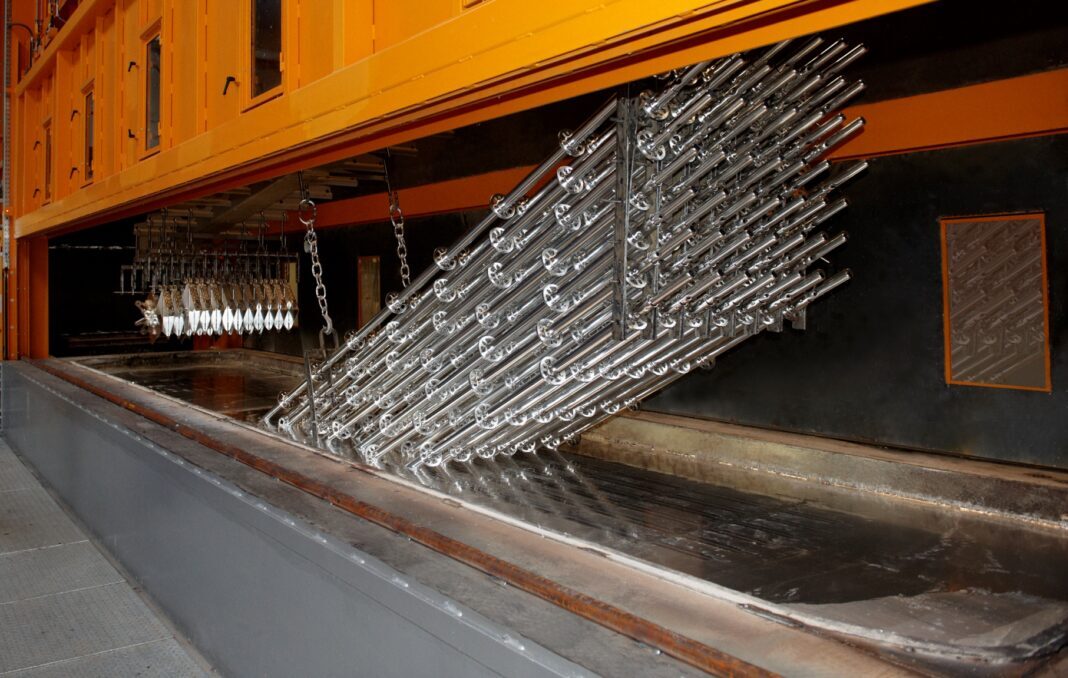
THE importance of safety, versatility and cost effectiveness relating to the use of scaffolding is not in dispute. Every installation – from building and construction to specific sectors such as offshore, rail and industrial maintenance – has to meet the highest standards in these key areas.
Sean Pike, UK MD of system scaffolding, access and weather protection specialist, Layher Ltd, says there is a ‘further dimension’ which is being highlighted by manufacturers, contractors and end users alike. He explained, “Optimising environmental performance has now become a factor that is not only called for by our customers but one which, vitally, we demand of ourselves.”
The view taken by Layher reflects today’s greater emphasis on the achievement of greener performance. This, the company believes, impacts not only on the broad need to ensure its methods always take account of environmental effect but also on the advantages that can then be realised from a competitive point of view.
“Every aspect of our activity now accommodates this consideration – from manufacturing and production processes to optimising our broad association with local, national and international communities,” Sean Pike added.
This philosophy at Layher extends to both economic and ecological sustainability. The organisation revealed it ensures, for example, that it utilises resource-preserving production processes and also focuses its commitment on areas such as facility construction and transport. “For example, we have created a dedicated energy management team at our manufacturing plant near Stuttgart,” Pike added, “which uses the international standard ISO 50001 as the basis for all activities and processes that call for the use and consumption of energy.”
Layher has identified several areas where the obligations associated with environmentally responsible activity should be applied. The sustainability of its production processes, the means of measuring performance and the design of the products themselves, all come under the green spotlight.
Pike said, “We have committed to a 10% reduction in energy consumption across our production processes over the next ten years. This includes a move towards optimising movement between manufacturing locations to help reduce CO2 emissions, the acquisition of raw materials that themselves are ecologically sustainable and the use of machinery which operates within the highest energy efficiency class.” The use of new production technologies and processes that look to ensure the preservation of resources can also be seen through the company’s focus on utilising technology such as combined heat and power and heat recovery facilities.
“It is vital that this approach is continually subjected to a reliable means of measurement,” Pike continued, “not just in order to demonstrate our performance, but also to identify areas where further improvements can be made.”
Targeting building refurbishment plans – ranging from regular roof repairs to the use of new innovations such as roll-up door products that are said to provide faster, more energy efficient operations – are cited by the company as good examples in this context. Pike added, “Replacing diesel forklift trucks with electric alternatives, installing photovoltaic systems and incorporating green spaces in new building plans are all factors that we apply and adhere to wherever possible.”
The business is also focused on a reduction of waste materials, often to create an alternative energy source.
Layher has taken steps to optimise environmental performance at its manufacturing plant – its new galvanising facility, for example, creates emissions that the business revealed actually have a beneficial effect on its surrounding woodland location. Product design is also on the sustainability agenda, for example, being able to combine new equipment with existing materials and stocks to help optimise the long-term use and versatility of scaffolding, weather protection and access solutions. It is a view echoed by Layher’s commitment to ensuring equipment approvals remain applicable across successive design generations.
“The use of lightweight materials also plays an important role not only by helping with operations on site but also because they can contribute to minimising transportation needs – with, again, a beneficial impact on emissions,” Pike added.
One recent development has been Layher’s Scaffold Information Modelling (SIM) software, which also brings environmental gains. Pike explained, “The design tool, which interfaces directly with BIM, provides a highly versatile planning method which offers enhanced presentation opportunities, communication with mobile devices via cloud-based mixed reality and even VR-modelling.
In turn, this can reduce the need for multi-party meetings and operations which, once again, can help cut down on travel requirements and consequent emissions. The focus on environmental performance – in all its aspects – is, today, high on the agenda of all responsible companies and, in our sector, we believe we take a committed and proactive approach to the issue. This year marks our 75th anniversary since we began the production of ladders in little more than a small hut and throughout that time, our belief in quality, innovation and working closely ‘in partnership’ with customers has been well recognised. This is now being enhanced by our belief in meeting our green obligations.
“Through our head office in Letchworth and satellite depots located not only in Scotland but also in Yorkshire, the West Midlands and Ireland, we demonstrate this approach on a clear basis and believe it goes hand-in-hand with, for example, maintaining stock levels and support during the current challenging times. The added emphasis we place today on optimising our, and our customers’, environmental performance will be recognised and appreciated, I am sure, by all concerned.”