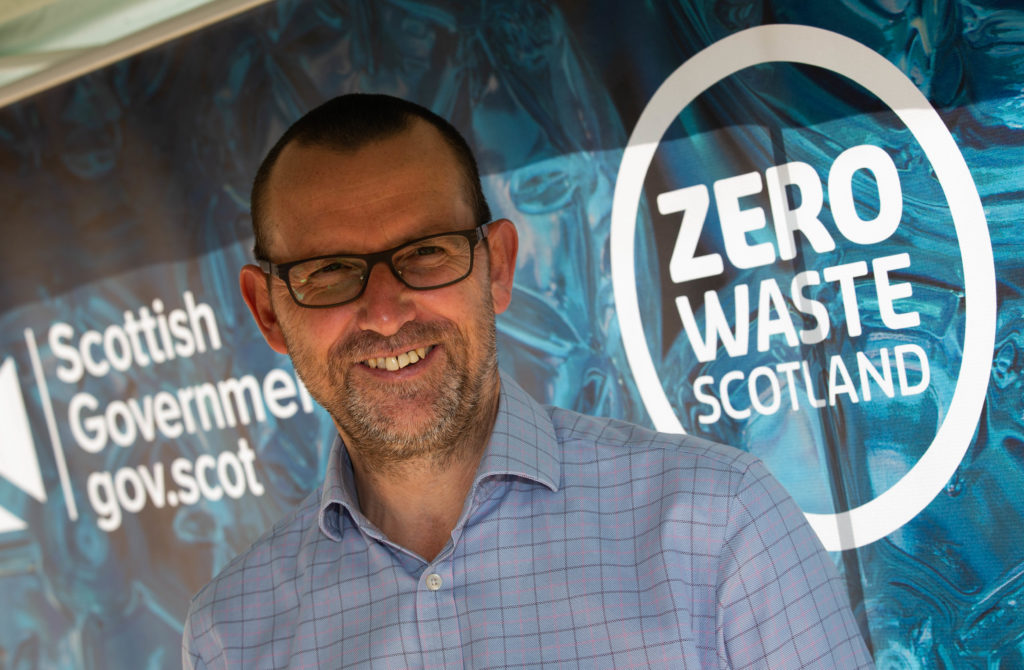
SCOTTISH construction businesses are being advised that the time for talking about sustainability ‘is over’ and action is required now to embrace circular economy aspirations and tackle environmental concerns.
Zero Waste Scotland has identified four ‘priority areas’ for the sector where opportunities exist to develop a more circular approach: designing out waste; purchasing power; on site activity; and digital innovation.
Iain Gulland, chief executive of Zero Waste Scotland, told Project Scotland, “Sustainability is not a new topic of conversation in the construction sector but as we navigate our way through the current climate emergency, the move from discussion to urgent widespread action is needed. Embracing the circular economy and tackling environmental impacts is no longer a ‘nice to do’ but crucial for businesses to build resilience and ensure long-term profitability.”
Gulland said that at the design stage of a project, there is an opportunity to build in sustainability ‘from the ground up’. He added, “Circular economy principles can easily be integrated to minimise a build’s carbon footprint, and more and more developments involve designing out waste, keeping materials in use, and regenerating natural systems.
“Embracing an approach like the ‘layers’ concept – in which different elements within the same building are designed so that they can be replaced without affecting the integrity of others – can lower the short and long-term environmental impacts of a build. Plus designing for adaptability with the ‘loose fit’ concept helps to extend the lifespan of buildings.”
Gulland explained that firms can also give materials a ‘second life’ by repurposing parts of previous builds into new ones. This can also have financial benefits in that valuable components can be kept in use rather than discarded.
In terms of purchasing power, Gulland said it is “clear” that the introduction of a circular approach early in the development process can “yield the best results”, even if realising these benefits in practice can be challenging.
Calling for greater collaboration to integrate sustainability into procurement, he explained, “Specifying a commitment to reused materials when you issue and respond to tenders, designing for ease of repair and deconstruction, and communicating clear expectations to staff and contractors when it comes to environmental impact can all help ensure your good intentions translate to positive results.
“Successfully embedding sustainability into procurement can also eliminate any risks associated with delivery across an extended lifecycle, as well as adding value. By ensuring they are measurable, reportable and replicable we can drive a step change – not just at an organisational level but across the wider sector.”
Gulland said managing waste on construction sites was one of the first areas the sector embraced to help reduce environmental impact. He added that the “true cost” of waste is still often underestimated when material and labour costs are factored in, highlighting figures that suggest 13% of raw materials ordered are discarded unused.
“Simply put, best practice waste management and material efficiency on site saves money,” Gulland said. “It can also maximise the value of surplus building materials, minimise site compliance risks, and strengthen your business’ reputation. With repeated warnings about the climate emergency, not to mention current economic pressures, good waste management on site really is non-negotiable for any business with plans for the future.”
Like many sectors, construction is currently undergoing something of a digital revolution. Gulland said embracing virtual tools can have a “transformative effect”.
“Building Information Modelling, along with augmented and virtual reality programmes, can help us visualise and test designs more effectively – using data and interactivity to help users reduce waste,” he explained. “Developing a ‘digital twin’ for a building is a great way to see how different sustainable modifications will perform and select the best fit. The virtual version will also mirror any changes to the physical building throughout its lifetime, so real-time data is always available to inform decisions.
“When it comes to innovation, off-site manufacturing and modular construction are also becoming increasingly common in Scotland.”
Despite “endless” opportunities to embed greener measures into the construction industry, Gulland warned that the timescale is “finite”, with potentially as little as ten years to mitigate predicted levels of global warming.
Zero Waste Scotland’s circular construction team can offer support to help companies move towards more circular business models. The organization also has a range of free construction guides available online covering a range of topics.
• To access the guides, visit www.resourceefficientscotland.com/Construction