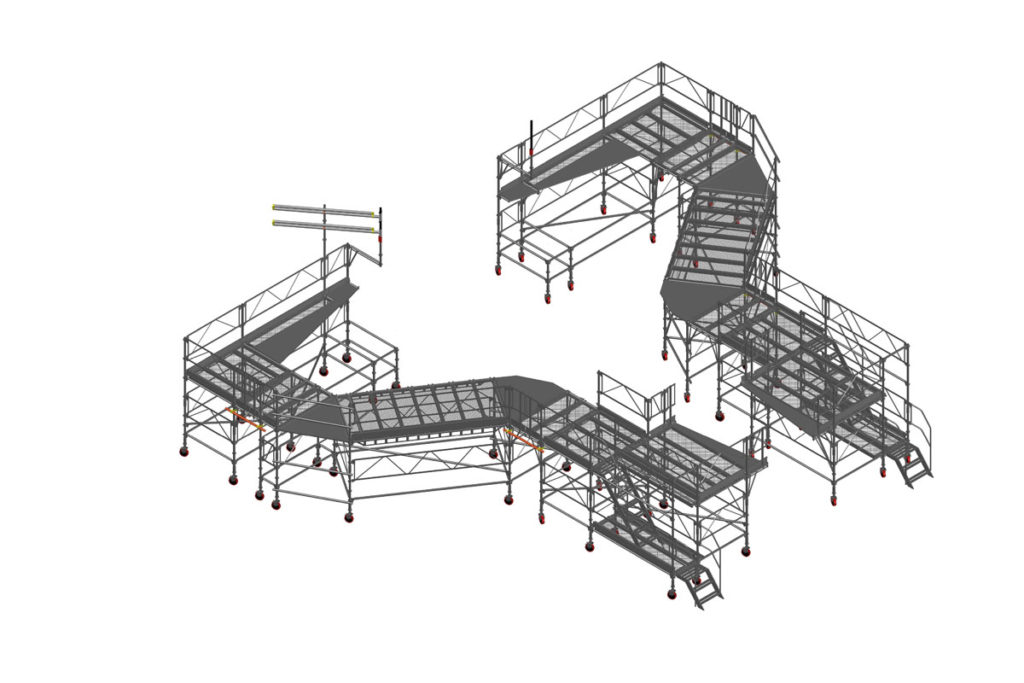
GLASGOW-based Turner Access is continuing to expand with projects in the defence sector.
The scaffolding firm has divulged details of its recent involvement in the Joint Strike Fighter Program, an initiative to replace a wide range of existing military aircraft for the US, UK and allies with the F-35 Lightning II. The F-35 Lightning II is a fighter jet range that has been developed by a number of leading aerospace companies around the world.
Turner said procurement of the F-35 system in the UK includes most of the required support equipment included as part of the Joint Striker Fighter Program; however, it does not provide a full Wrap Around Maintenance Staging (WAMS) solution. This is required for regular inspection and servicing by the main operating base.
Defence Equipment and Support (DE&S) contracted Aviation Spares & Repairs to supply the WAMS solution for the F-35B airframe. Turner Access was subsequently sub-contracted to provide the aircraft docking platforms.
The WAMS solution needed to provide a safe working platform for personnel to work at height for prolonged periods of time. Turner’s OCTO system scaffolding was used to provide the WAMS application.
Turner OCTO System is described as being designed to improve safety, with features manufactured into key components including ergonomics, visual safety checks and a safe system of work to prevent the risk of fall from height.
The WAMS requirement was for a modular system to allow for easy storage when not in use. Turner explained that a series of tailored docking modules were designed and manufactured to provide a wrap-around solution for accessing specific areas of the F-35 aircraft. This included the top of the wings and fuselage, the tail and nose. The project requirements were for ten docking units in total, made up of seven modules linked together to provide the wrap-around staging. The docking structures provided a single level platform with walk-through access.
Any part of the structure that might have come in contact with the aircraft skin or be adjacent to it had to be covered with non-marking protective buffers.
Training on safe manoeuvring of the docking structures and minor adjustments was also required as part of the WAMS provision.
Turner said the first major challenge was the design of the docking platforms. Due to F35/JSF program security controls, aircraft dimensions, specifications and drawings cannot be released.
This meant that the Turner Access designers had to rely on PDF outlines and reverse engineer sub-structure frame drawings to incorporate them into CADS software in order to design the structures. During the design phase, specific locations also had to be considered for air, electric and bonding connections.
The WAMS solution had to be manoeuvred close to the airframe, therefore there were a number of critical angles to negotiate. In most locations, the upper surface of the airframe had to be accessed by a platform that was no further than four inches from the external profile of the aircraft.
Special decks had to be designed and manufactured. Turner’s manufacturing facility produced bespoke special decking units to allow the WAMS to be positioned next to the aircraft without substantial gaps.
Another challenge surrounding the installation of the docking structures was the requirement to be FOD (Foreign Object Damage) compliant. To ensure no parts could ever loosen, nyloc nuts and bolts were installed, along with other measures.
Turner said the combination of design, service provision and training, along with the firm’s relationship with Aviation Spares & Repairs, resulted in a successful project being delivered.
Bill Watson, sales and marketing director at Aviation Spares & Repairs (ASR) said, “ASR has been a trusted supplier to the UK Ministry of Defence for some years and when the prestigious opportunity to provide Wrap Around Maintenance Systems for the newly acquired F-35B aircraft was released, it was an opportunity that was too good to miss.
“Being a supply chain management specialist, ASR clearly needed to find a partner that could support the conceptualisation, design and fabrication of a suitable system. We approached Turner Access having been involved in a similar project for a different airframe some years earlier and after a preliminary discussion, agreed to pursue the opportunity together. As is often the case, the project has been more demanding than initially anticipated, with a number of major decision changes testing the resourcefulness and adaptability of the team to the extreme and a delivery programme that also proved to be challenging. ASR is proud to have worked alongside Turner Access in what has become a very close and open relationship. It is hoped that having delivered a system that is fit for purpose and is now effectively available ‘off the shelf’, there will be opportunities to supply similar systems to other operators of the F-35B.”