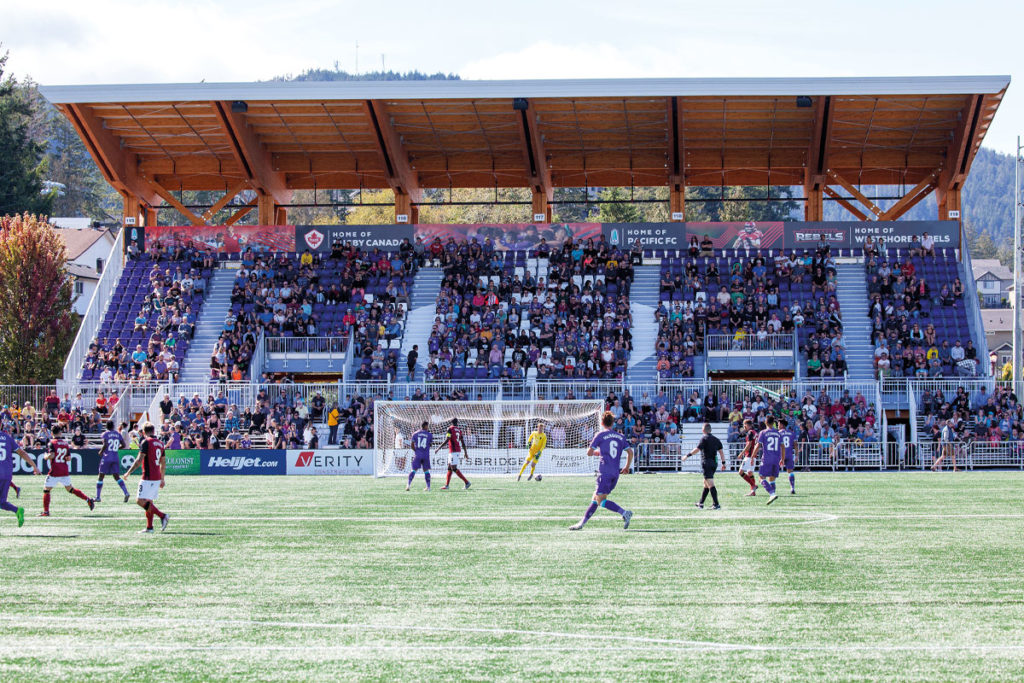
JAIME Manca di Villahermosa founded Bear Stadiums, an Italian company specialising in wood modular systems for sport infrastructure, in 2016. Previously the lead architect on the rebuild of a football stadium in Caligari, he completed further work on the renovations of Frosinone FC and Brescia FC’s arenas. Now with his own company, he says he can deliver a 20,000 seater stadium in just seven months.
Jaime recently told Project Scotland about his company’s build of the 6,000-capacity Westhills Stadium in Victoria, Canada.
The key to the short time frames is modular building using a laminated type of wood called glulam. The different pieces of the stadium are manufactured offsite then shipped to the area of land in which the stadium will stand, before being pieced together according to the design agreed with the client. A local contractor is used to lay the foundations for the stadium, before Bear Stadiums and partner, Rubner Holzbau (Rubner), move in to piece together the wood shipped from northern Italy.
“The specialised worker who will be in charge of the assembly has a very simple job – it’s like Meccano, the holes are already there, they just need to stick the bolts in the right hole and put it together,” Jaime explained.
In preparation for the 1990 World Cup in Italy, Rubner headed the redevelopment of the East Stand in the Stadio Olimpico in Rome, with Jaime saying the stand is made ‘almost entirely out of glulam’ apart from the cement pillars.
He insists that Rubner is one of the finest glulam wood producers in Italy, with over 100 years experience in developing wood technology and engineering.
Despite Rubner’s heritage and acclaim in the wood industry, it is an obvious eyebrow raiser to use such a build material for football stadiums. As Jaime acknowledged, in 1985 tragedy struck Bradford City FC when 56 spectators lost their lives after a wooden stand in the club’s stadium caught fire.
“Since the Bradford fire there has been huge focus in many aspects of stadium design and project, so what we’re leading up to is our stadiums are absolutely safe, otherwise they would not pass the fire regulations that are extremely strict – and rightly so. Other than the glulam structural elements, all materials used, such as seating solutions, roofing panels, stairs and rails, are carefully selected to guarantee state-of-the-art safety standards.
“Our stadiums have an evacuation time of between seven and fifteen minutes. Every person within the stadium has to be able to reach a safety staircase and exit between that time. The exits are designed to be wide enough to allow the flow of the crowd to exit.
“The structural elements are designed so that their structural resistance is not put into peril in the case of fire, meaning that the rate at which the glulam beam will burn is a tenth of a millimetre per minute. So what you do is you plan the cross-section of the beam to be over-dimensioned in order to guarantee at least one hour of evacuation time before the structure could potentially be subjected to collapsing – which is not the case with cement or steel. Cement or steel will collapse much faster and in a less controlled way.”
The advantages to using glulam wood on the build of stadiums, Jaime said, are that the lightweight material not only ensures safe, quiet and tidy construction but mitigates the risk of damage caused to the lower areas of the stadium from shaking forces due to the stadium being at its lightest at the highest points.
Furthermore, he notes that the interior spaces under the stands – commonly used as changing rooms, physio rooms and gym areas – are naturally insulated, so very little energy is needed to heat and cool them. Jaime added that the stands experience similar high levels of insulation.
The wood, however, only allows for a capacity of between 1,250 and 20,000 – any more than that and a hybrid system of wood and steel or concrete is needed to ensure the safety of the structure.
Wood on its own, however, is still able to pass the strict FIFA and UEFA standards that clubs must comply with in order to compete in their domestic leagues and continental competitions.
“An example, one of the standards we always put in place is the width of steps which we wish to maintain at 80 centimetres – this is a FIFA recommendation, but it is not a standard rule. We’ve seen in certain stadiums where the width of the step is reduced to 75cm. We insist on having comfortable seating and sufficient leg space in all our stadiums,” Jaime revealed. “Other aspects of the FIFA regulations insist upon is the comfort of the media area and having sufficient space for journalists and media within the stands dedicating a media room, and camera positions – these are all things taken into account when building stadiums.”
Jaime said he would be ‘thoroughly thrilled’ to build one of his stadiums in the UK. He says that he has liaised with English clubs about builds, but so far has not completed a project in the UK.
Only three years in, they have completed one stadium and constructed several stands – it remains to be seen if modular stadiums will become a part of the beautiful game.