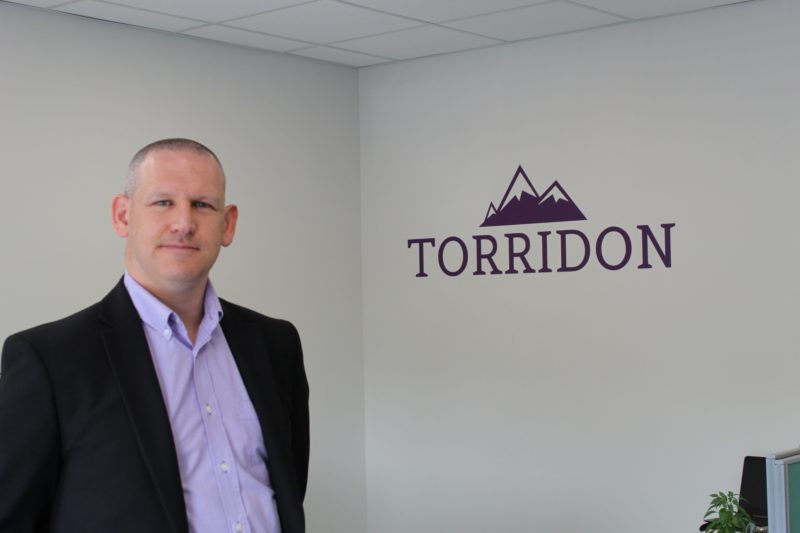
Kenny Telfer, chair of RICS Matrics Scotland, discusses the importance of collaborative value management
IN a time of political and economic uncertainly in the UK and Europe, along with increased pressures on our supply chain, what we need is a greater focus on collaborative value management in construction projects, eliminating unnecessary costs and delivering more for less.
Quantity surveyors are well placed to lead on this mission and should motivate the project team to reconsider the assumptions that are made during design and construction in search of more cost-effective ways of achieving the desired outcomes.
COLLABORATION
Let’s be clear here, we are not talking about squeezing an extra 1 or 2% discount from the contractor; all too often we have seen with disastrous consequences what happens when margins are squeezed with the demise of some well-established firms. Mark Farmer commented in his paper “Modernise or Die” of the need for greater collaboration in the construction industry. In my own business I have established methods of value engineering which give consideration both at a design team level and by involving the expertise of the contractor, something which is all too often overlooked, which have brought about real successes on our projects to date. We believe that it’s the marrying up of the design-led solution with the buildability expertise and utilisation of supply chain relationships of the contractor in which real added value happens on projects and this is adding to our growing reputation in this important field.
LEAN
I have been involved in the implementation of lean process improvements using the famous Toyota lean production principles whilst working as a manager in a national housing association, something I went on to write about in my dissertation at university. I have long held a fascination with exploring ways in which things could be done better, faster, more efficiently, delivering more for less. Now as a company director with Torridon CPM I’ve made it my aim to carry this learning into the projects to ensure that our clients can benefit from the learning behind lean thinking.
When we think about lean in the construction industry we think about offsite construction and the like but fail to recognise the simple but beneficial effects of carrying out a lean review of our own administrative processes. In one improvement event I participated in, we cut down our time to pay invoices by 30 days through simple but effective processes, mapping each stage and the actions taken to see where savings could be made in time, cost and where quality could be improved. This resulted in better deals being struck with suppliers who were all too happy to take payment much sooner in return for larger discounts. We also reduced the amount of time each invoice took to process saving administrative costs in the finance department. In another event we reviewed the teams we had in place delivering bathroom adaptations within the existing housing stock. By training staff on some key elements, we were able to reduce the reliance of one specialist trade and therefore improved the programme and reduced costs for delivering these adaptions, all at a time when grant funding was being cut.
Offsite manufacture will play an important role in the future of the industry, as the winter storms of earlier this year showed when production dropped significantly during the snow. The thing about this magnitude of change though is small contractors will continue to build and maintain property without those changes for many years to come. Let’s face it, Jane’s Joinery Ltd who builds 20 units a year for multiple clients isn’t interested in offsite necessarily. We need other aspects of value management to be implemented on small scale businesses.
DISRUPTIVE TECHNOLOGY
As a board member of the RICS Matrics UK Board I get involved with promoting the profession and inspiring the next generation of surveyors, from schools and university visits to meeting graduates and APC candidates at events. One thing each group have in common is the clear understanding that technology is about to significantly disrupt industry. We have entered the technological age without a doubt and many jobs will be lost across a host of industries as a result of this type of innovation. Automated taxis and trucks, drone delivery vehicles, automated brick laying machines and 3D printed homes are just some examples of how this technology is moving. Traditionally the construction industry has been slow to respond to these changes, but I believe our next generation will grab the bull by the horns and drive this change through innovation and embracing new technology to enhance the services we deliver.
We don’t need to wait for flying taxis to appear on our streets before we embrace change though. Already we have project management apps that assist with sharing of project documentation and management of change on our phones and tablets. Cloud apps are great for sharing and collaborating with the design team, where these are updated and managed correctly.
Torridon CPM invested in BIM-ready cost management software to streamline the way in which cost plans are produced and updated through to post-contract valuations of completed works without the need for significant reinvestment of time and energy redoing work. Measurement is done electronically from CAD drawings or PDFs eliminating the need to print, and also providing a clear log of what exactly was measured on a particular element. Professional reports are produced at the touch of a button, and without the need for line by line analysis of formulas in spreadsheets. Our software allows us to overlay previous drawing revisions over new revisions and instantly points out the changes made through colour differentiation. No more endless hours squinting over drawings playing spot the difference! It is these type of administrative savings that are crucial at this stage for SMEs, not necessarily the offsite production and BIM-compliant projects that are going to make immediate differences to the vast majority.
CONCLUSION
Change is being driven down from national government agendas and modern technology is finding its way into the industry. We as industry leaders need to act now to embrace this change and influence the way it will improve our industry for the better. Those involved in construction projects should not only look for ways in which a collaborative environment will benefit the project and therefore the client but should also carry out systematic reviews of their own processes. We need to reduce administrative burdens in order to reduce costs and increase margins. We need to deliver more for less.