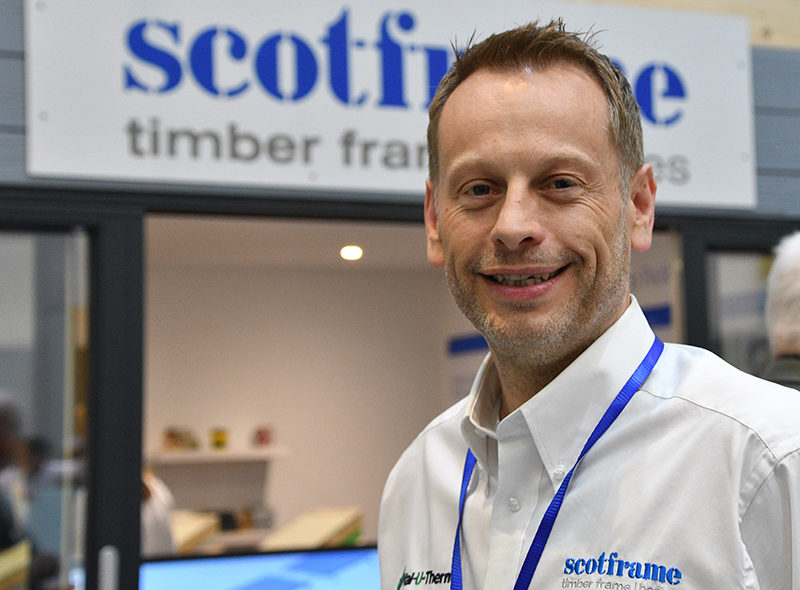
By Malcolm Thomson, sales director, Scotframe
IT is predicted that the UK needs around 300,000 new homes every year for the foreseeable future, to tackle the housing shortage. That’s a staggering challenge, not just because this is such a huge number, but because these homes can’t be just any old houses. They should also be energy efficient, have as low an environmental impact as possible, and if they are going to alleviate the problem, many must also tick that all-important ‘affordable’ box.
Meeting this challenge is being made even tougher by low productivity in the construction sector, and a skills and materials shortfall which is only going to be worsened by Brexit.
In my opinion, we can’t meet this target using traditional construction methods alone – we must also take full advantage of offsite manufacturing techniques. As a director of a company specialising in offsite timber frame packages, I would naturally say that. But my views are backed up by the UK Government, who in its autumn 2017 budget, said that it would favour offsite manufacturing on all publicly funded construction projects from 2019. That’s because the government has seen the myriad of benefits offsite construction offers. The House of Lords Science and Technology Committee has also recently taken oral evidence from housebuilders and engineers on the potential benefits of off-site manufacture in terms of building high quality, affordable housing.
Offsite is experiencing rapid growth – the industry is worth around £1.5 billion in the UK alone and is projected to rise to £6 billion by 2025. This reflects the fact that construction companies are finally cottoning on to its many advantages. Homes can be built faster and to a higher sustainability standard when compared with traditional construction methods, making them more cost effective to build and live in. This has the extra bonus of addressing the issue of fuel poverty, as residents will benefit from reduced heating bills.
Delivering homes under factory conditions offers a clean working environment that is unaffected by weather, improving productivity and enhancing quality and safety. It also addresses the problems caused by our industry’s ongoing shortage of skilled workers, because offsite construction doesn’t require such a large workforce. It provides local jobs for local people and offers an opportunity for apprenticeships in design, manufacturing and building.
Scotland leads the way in timber frame construction, with 83% of new build Scottish homes using timber frame, compared to just 23% in England. This could partially be explained by timber frame’s impressive thermal performance, which is particularly welcome in Scotland’s colder climes. Timber frame is also a particularly attractive option for self-build, which has always played a larger role in Scotland. But self-build is now growing in popularity south of the border, thanks to the recent Right to Build legislation.
According to the Structural Timber Association, the market share for timber construction in England is steadily rising, helped by offsite technologies such as cross-laminated timber and structural insulated panel systems. The clear majority of UK homes may still be built using traditional masonry, but with a shortage of site skills and the rising cost of materials, even the biggest housebuilders are likely to start considering using timber frame more frequently in the near future.
Since Scotframe started out in 1989, we have expanded steadily and now have a £35 million turnover, 160 employees and have just launched a new showroom in England. Last year the business was acquired by the global group Saint Gobain, and we expect this to help accelerate our expansion into markets south of the border.
So, if England’s housebuilders need any advice on how timber and offsite techniques can help them build high quality, cost-effective, sustainable, energy-efficient homes more quickly, I would encourage them to look north of the border to the wealth of knowledge and experience that Scotland has to offer.