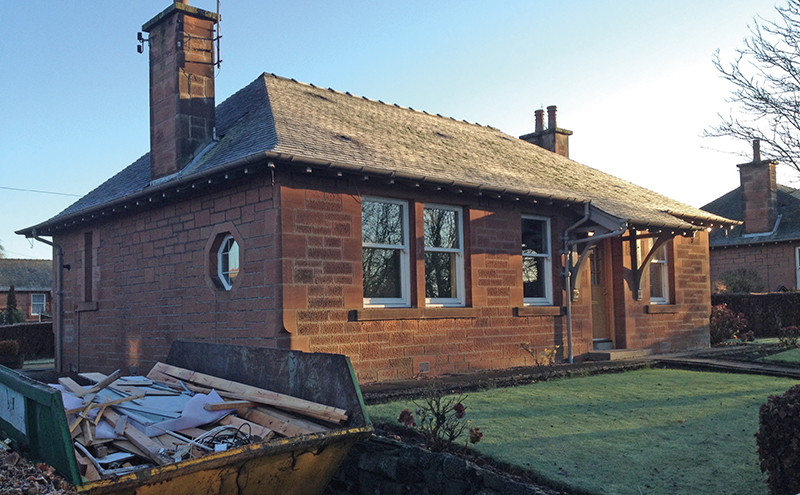
Paddy Leighton, director at Icynene UK, discusses how trials using spray applied insulation have proved successful in historic and difficult to treat buildings in Scotland
MODERN buildings are constructed to standards of thermal efficiency that are a world apart from those our Victorian ancestors lived and worked in.
However, records show that over 20% of current housing stock was built pre-1919 when energy costs were far lower than today and measures to prevent heat-loss through walls and roof were rarely considered.
The UK has a rich heritage of architecturally significant properties, many of which have listed status and, under European Regulations no less than 400,000 historic buildings are required to be insulated to a standard appropriate to achieve energy and carbon savings.
With energy use in domestic buildings accounting for roughly a quarter of carbon emissions in the UK, research suggest that the best way to reduce energy consumption and heating bills is to improve the energy efficiency of the building.
In older, and in particular architecturally significant buildings, improving energy efficiency through heat–loss mitigation presents a particular challenge.
Many of these “difficult to treat” buildings were built of solid wall construction with hard plaster applied directly on to the interior face of the wall.
In others, soft, lath-and-plaster skins set off the external wall on timber spacers were installed. These, together with internal timber panelling common to many higher value buildings creates something similar to a rudimentary cavity wall type of construction. Interestingly, it is often the internal finishes of buildings as much as the external structures that influenced their elevation to listed status.
Consequently, invasive measure to install insulation materials has been strongly resisted to prevent potential damage to delicate and irreplaceable interiors.
Insulation trials on difficult to treat buildings
In Scotland, trials to assess the potential of a new type of injected foam insulation have been under way for some time on two “difficult to treat” properties.
Bogendollo House, Aberdeenshire
The first trial took place in 2011 at Bogendollo House, an early 19th century category C Listed Building of solid wall construction with internal, lath-and-plaster lining, located near Fettercairn in Aberdeenshire.
The work was funded by the European Regional Development Fund and the Scottish Government’s SEEKIT Programme under the Construction Improvement Club (CIC) scheme.
The project was undertaken as a collaboration between academics at Robert Gordon University’s Scott Sutherland School of Architecture and Built Environment in Aberdeen, Heriot-Watt University in Edinburgh, local architect consultants and industry partners Icynene, suppliers of the insulation system and locally based conservation contractors, Kishorn Ltd.
The Icynene insulation is a spray applied system that expands quickly but gently, sealing all gaps, service holes and hard to reach spaces, virtually eliminating cold bridging and air leakage.
Unlike the urethane foams of 20 years ago, modern spray foams such as Icynene uses water as the blowing agent. This means that the reaction between the two components produces C02 which causes the foam to expand. Cells of the foam burst and the CO2 is replaced by air.
This “open cell” foam provides outstanding insulation properties but still allows the building to breathe naturally.
Icynene was developed in Canada and is now gaining popularity in Scotland and other areas of the UK in both the domestic and commercial sectors.
The Bogendollo project was led by Dr Amar Bennadji, principal investigator and lecturer in Architecture at Robert Gordon University. He explained, “At Bogandollo House, the insulation was injected into the narrow void between the external walls and the lath-and-plaster lining.
“The foam expands slowly and puts little pressure on the fragile inner walls.”
Since the trials at Bogendollo began in 2011, performance monitoring has been continuous and has shown positive results. Dr Bennadji continued, “Following the trial, the heat loss through the wall was reduced by approximately 50%. We believe this project opens the door for both historic buildings and older domestic properties to finally retain warmth, reduce their energy bills and contribute towards efforts to curb global warming by reducing their carbon footprint.”
Gannochy Trust Perth
Icynene insulation has also been used in trials on a property in Perth, owned and managed by the Gannochy Trust.
The property is one of an estate of detached cottages built between 1923 and 1931 by AK Bell of the Bells Whisky family.
Icynene was installed as one of the suite of thermal interventions for traditional and historic buildings developed by Historic Scotland, as part of the Energy Efficiency Research Programme that has been running since 2009.
The property treated was built in 1927, with mass walls of cement-bonded red sandstone approximately 500mm thick. Colliery brick was used for some internal partitions, and they were finished with lime plaster directly onto the brick.
The external walls and ceilings were lined internally with lath and plaster, creating a small cavity of approximately 40mm between the inner face of the wall and the lining.
To minimise loss of internal space it was decided to retain the existing linings and apply blown materials behind the existing finishes.
Initially, blown cellulose was to be used but specialist conservation contractor Kishorn Ltd, proposed that Icynene’s open cell insulation should be injected into the cavity behind the lath and plaster.
While this approach was considered unusual, tests by Glasgow Caledonian University had shown it was a very vapour-open material and therefore would allow the dissipation of any wall humidity through evaporation and diffusion.
To inject the material required the drilling of many holes, approximately 25mm in diameter normally at 1 metre centres.
Preparation for the installation of this product was extensive. It involved the removal of existing wall coverings and skirting boards, plugging of the junction between the timber ground for the plaster and the masonry and sleeving of the mains electrical cable from plug boxes on the wall.
However, with these preparations complete, the actual installation was relatively straightforward.
An infra-red camera was used to check that the foam had spread evenly into the void and once the material had set, the holes were patched over and skirting boards refitted.
Work was completed in February 2015, giving time to conduct basic heat flux measurements in the finished building.
To obtain an average value, four heat flux plates were mounted on the wall in one of the bedrooms.
The measurements were then compared with those taken the previous autumn, as well as from a similar property close by.
The U-values showed good improvement in all areas. This monitoring will continue over a three-year period to fully assess the effects of the wall insulation.
Where does spray applied insulation fit?
Spray applied insulation is broadly cost-neutral to other types of insulation. This, together with its speed of installation, minimal waste and its ability to perform in difficult to treat applications and the fact that it can be injected into voids that would otherwise require invasive tear-out of surfaces, means spray foam is an attractive and cost-effective solution, for many historic structures.
Its non-invasive installation methods can also allow the continued occupation of the building with the minimal of disruption to users and negligible impact to the fabric or the breathability of the structure.
A final comment
The report on the insulation trials at Bogendollo House was published in the International Journal of Low Carbon Technology. Since publication, Dr Bennadji has received enquiries from parties wanting to learn more about the techniques used in the project.
“Even now, in early 2018, more than six years after the report was published, people contact me for guidance on these new and exciting methods of insulating old properties. The Bogendollo project really is an excellent example of how Co2 emissions can be reduced to meet the UK’s target of 80% reduction by 2050,” said Amar.